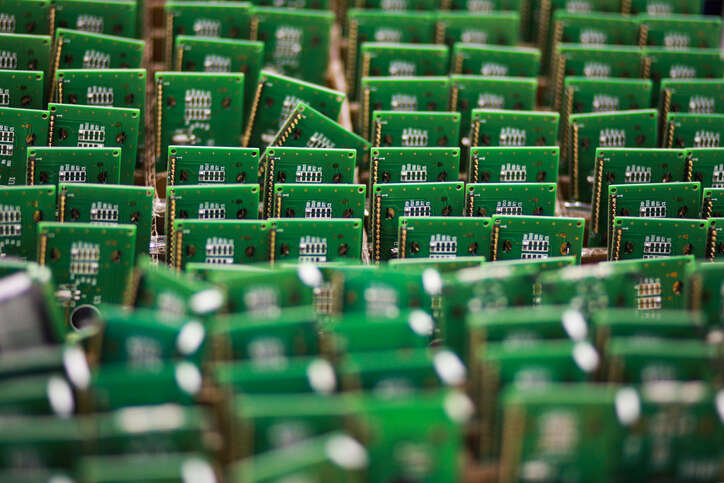
Business leaders are optimistic the global chip shortage is coming to an end after two years of heavily restricted supply of semiconductors. But despite some improvements in the situation, analysts believe supply issues could continue for months and even years to come, particularly for cheaper components manufactured on older technologies which are not receiving investment from chipmakers.

The chip shortage was initially sparked by the Covid-19 pandemic, with the widespread switch to home working causing a sharp uptick in demand for laptops and consumer devices, while other industries such as the automotive sector paused or cancelled their chip orders.
With production in these industries now ramping up again, companies have found themselves at the back of the queue for components, causing factories around the world to cease production for days or weeks at a time. But now it seems as if the situation may be improving.
Chip supply situation improving, say manufacturers
On Thursday three manufacturers in different sectors reported their financial results, with executives commenting that the chip supply situation is improving.
Korean automaker Hyundai, which owns brands including Kia, posted its best financial quarter for eight years, having seen demand for its high-margin SUVs rocket. Hyundai told investors that the easing of the global chip shortage means it has been able to resume offering overtime and weekend shifts to staff at its factories, and says it will be able to step up production in the second half of the year to meet demand.
ABB, which makes robotic and control systems for manufacturers and automotive companies, also sounded optimistic as it reported its second-quarter results, saying it has seen a 20% year-on-year increase in the number of orders placed in Q2, and that the improving semiconductor situation would allow it to fulfil these in the second half of the year.
“Overall, the supply chain constraints slightly eased compared with the previous quarter,” ABB CEO Bjorn Rosengren said. “We anticipate further easing of component supply in the coming quarters.”
Meanwhile, Electrolux, the biggest supplier of home appliances in Europe, is also looking to a future where it will have its chips. It missed its second-quarter earnings target as the global economic downturn and the conflict in Ukraine hit its revenue and profits, but said the future of its supply chains is looking promising. “Step by step we are coming back to a more normalised supply environment,” CEO Jonas Samuelson said on the company’s earnings call.
So is the global chip shortage over?
As reported by Tech Monitor, this new-found optimism around chip supply could be partly because demand is decreasing. Memory chipmaker Micron downgraded its financial forecasts last month on expected falling demand, causing other chip stocks to fall. The wider economic situation could also see companies such as TSMC, Samsung and Intel scale back previously announced plans to build new chip factories and diversify the global supply chain.
The war in Ukraine is likely to constrain the supply of gasses needed in the chip-making process, extending the chip shortage, IDC analyst Vinay Gupta said this week. Russia and Ukraine are the two biggest suppliers of neon, a gas used to produce semiconductors, and Gupta, IDC’s research director for Asia Pacific, told CNBC: “The semiconductor supply is not going to increase immediately. There are a lot of raw materials, gases, which were required for production of those semiconductors.”
Intel CEO Pat Gelsinger expects the supply problems to continue into 2024 citing difficulties getting hold of manufacturing equipment.
Mike Orme, who covers the semiconductor sector for GlobalData, agrees that the industry is not out of the woods yet. He says shortages of chips made using older process node technologies are likely to endure.
“These are chips that cost cents and dollars to do such specific but vital jobs as acting as LCD drivers, power management controls and microcontrollers and sensors in edge of the edge IoT devices,” Orme says. “There is a shortfall in foundry capacity to make such chips which are nowhere near as profitable as making leading-edge chips for the makers of smartphones, servers or gaming PCs.”
Because there’s no money in old chips, Orme says manufacturers like TSMC are pushing clients to have their components produced on newer, more costly technologies. They want to “persuade their customers for trailing edge chips to use their more advanced process technology to make these chips at greater cost, while yielding them, though, better chip price/performance and lower power draw,” he says. “[TSMC] is already pushing clients to shift from its 40-nanometre node to 28nm as it’s not investing a penny on 40nm technology either to improve it or add capacity.”
At the other end of the market, Orme also foresees problems with the supply of the wafers on which leading-edge chips are designed and built. The biggest player in the wafer market, Sumco, says its supply of 200mm and 300mm wafers is sold out to 2026. These are used by TSMC and other manufacturers to make high-end chips for consumer devices and data centres.
“These are not commodity products but customer-specific products often involving hundreds of parameters, but it has not been a high margin business,” Orme explains. “Again, it hasn’t been profitable to add new capacity over the last several years.”