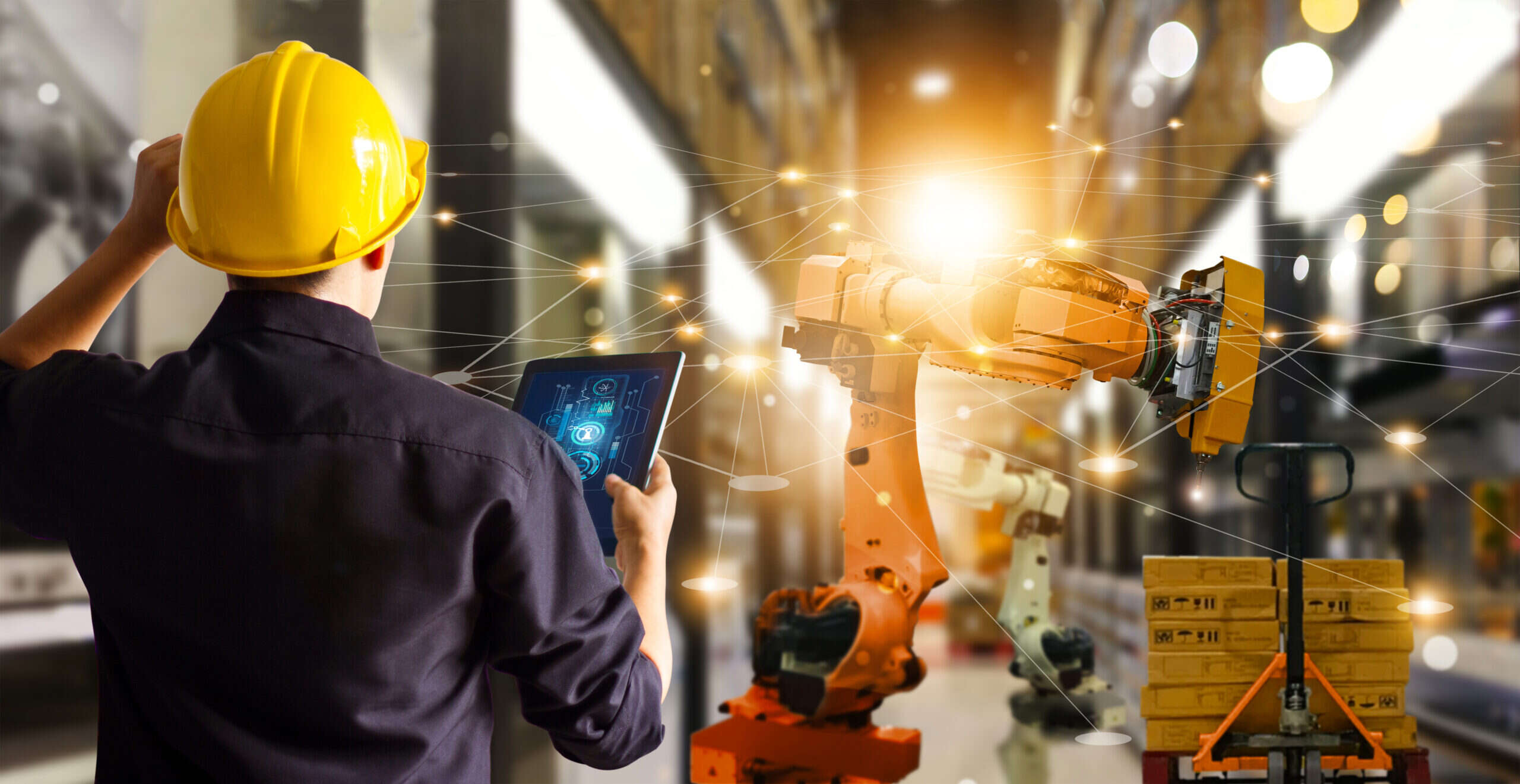
Although global supply chain issues are often discussed as mere after-effects of the Covid pandemic, a number of issues faced by those in logistics and distribution have been accentuated rather than created. Freedom of movement restrictions in the wake of Brexit, for example, and a discrepancy between China and the rest of the world in terms of AI adoption, are just some of the longer-term issues already affecting the distribution space.
As the business environment becomes more volatile in the wake of the pandemic, not to mention current trends in geopolitical instability, some manufacturers have started moving their production processes from Asia to Europe. This combination of factors, as well as the unpredictability of global fuel prices, has led to skyrocketing transportation costs for containers. This, in turn, has impacted supply chains making business agility and data insight more important than ever.

Indeed, according to Håkan Strömbeck, industry and solution strategy director for cloud software specialists Infor, inflated fuel costs are likely to pose the most trouble for distribution businesses over the next few years.
“Supply chain disruption is very dependent on the outcome of the war in Ukraine,” Strömbeck says. “It has contributed to longer shipping times, shortages in vital materials, and because the war has inadvertently led to a rise in fuel costs throughout the world, this is having a major knock-on effect on logistics more generally.
“Another problem is that in the intervening period between the worst of the pandemic and war breaking out, there was an emphasis on building up warehouse capacity and maintaining a higher level of stock. So while we saw an increase in the number of warehouses and distribution centres before, now inflation has surged and consequently the working capital costs associated with having a larger inventory footprint are much higher.”
Staff shortages and changing customer expectations
While Strömbeck strongly believes that digitalisation is the solution to many of the logistics industry’s problems, it can only go so far. This, he says, is because state-of-the-art hardware and software solutions need people to manage them, and with a shortage of expertise and dwindling staff numbers, distributors may find it difficult to make some of those digital transformations effectively.
“Staff are learning about tools faster than ever before,” Strömbeck says. “And because tech is so advanced now and UX such a key component of training, more people are able to learn about things which previously would have been in the hands of a few gatekeepers. Therefore, one of the ways that employers within the distribution space can deal with the problem of managing digitalisation effectively is to train more staff in the use of some key tools. They should also strongly consider utilising machine learning. By speeding up the laborious processes that once took months or even years to train staff on, machine learning has the ability to automate and deliver information to make even the most inexperienced employee look like they’ve been working in that area for decades.
“Instead of thinking about machine learning as a ‘replacement’ for different parts of the workforce, businesses need to shift their mindset to consider the advantages. Used properly, AI tools can function in an almost supervisory or mentor-like capacity. They can give employees the opportunity to, for example, upsell, cross-sell and see customer patterns of personalisation much more effectively than they might have in the past. At its base, AI allows for more focus on quality work, rather than being tied up in repetitive and laborious manual tasks.”
This focus on ‘quality work’ is key according to Strömbeck, since one of the major effects that the pandemic has had on the distribution space has been a major shift in customer demands and expectations. There is now more of an emphasis on personalisation, faster delivery, the proliferation of regional distribution hubs and availability in harder-to-reach areas, and ultimately, according to Strömbeck, digital investment can help to meet these new demands.
“You need to be fully aware about how your warehouse distribution centre delivers on each individual order,” Strömbeck says. “Making sure that you have the right volume of products available to actually distribute on an omnichannel basis; some of which might not be within your control. Then it’s about getting transparency from your different warehouses and distribution centres, especially now when several manufacturers are moving into direct delivery and bypassing distributors completely.
“What this comes down to is that if you don’t have control of your data and inventory, someone else will and they will end up eating your lunch. What distributors should be emphasising is the value-add they give which direct delivery from manufacturers does not. Cable-cutting in the electrical distribution industry, for example, or packaging for B2C ecommerce. These sorts of things are vital, and sometimes can even come with other services like the rental of tools in builders merchants for the construction trades, and data is crucial for identifying those specific customer needs and demand levels to ensure a good customer experience and build loyalty.”
The future of logistics after Covid
Strömbeck insists that if and when businesses make these changes, the difference becomes immediately clear. By shifting from on-prem data storage to cloud, logistics businesses can more easily identify trends, niche segments, and deliver more effective customer service to impact their bottom line.
The flipside, of course, is that if distributors don’t implement the kind of out-of-the-box functionality that Infor offers into their operating model, they are already potentially years behind competitors who do. And this, according to Strömbeck, means that they are giving away business opportunities and losing whatever competitive edge they may once have possessed.
“Distributors need to think more about the optimisation of fulfilment,” he says. “That is, how do you fulfil something taking different parameters into account? From cost efficiency to meeting expected delivery times, is your distribution business differentiated? You need to have razor-sharp data at your fingertips, and trying to do this manually is so much slower and so much less reliable than if you have digitised your offering in some way.
“Sustainability is also another emerging factor, since transport is such a central component of the distribution space. In order to achieve better environmental sustainability credentials, logistics businesses would be wise to consider augmenting their processes with AI, machine learning and being in the cloud. These trends drive efficiencies and can help with things like ‘reverse logistics’, whereby materials and products can be returned or re-furbished based on customer needs. Not only does this provide a cheap and easy way of combining cost-effectiveness with more sustainable practices, but it offers a key differentiation from manufacturers trying to move into the distribution space through offering value added services.”