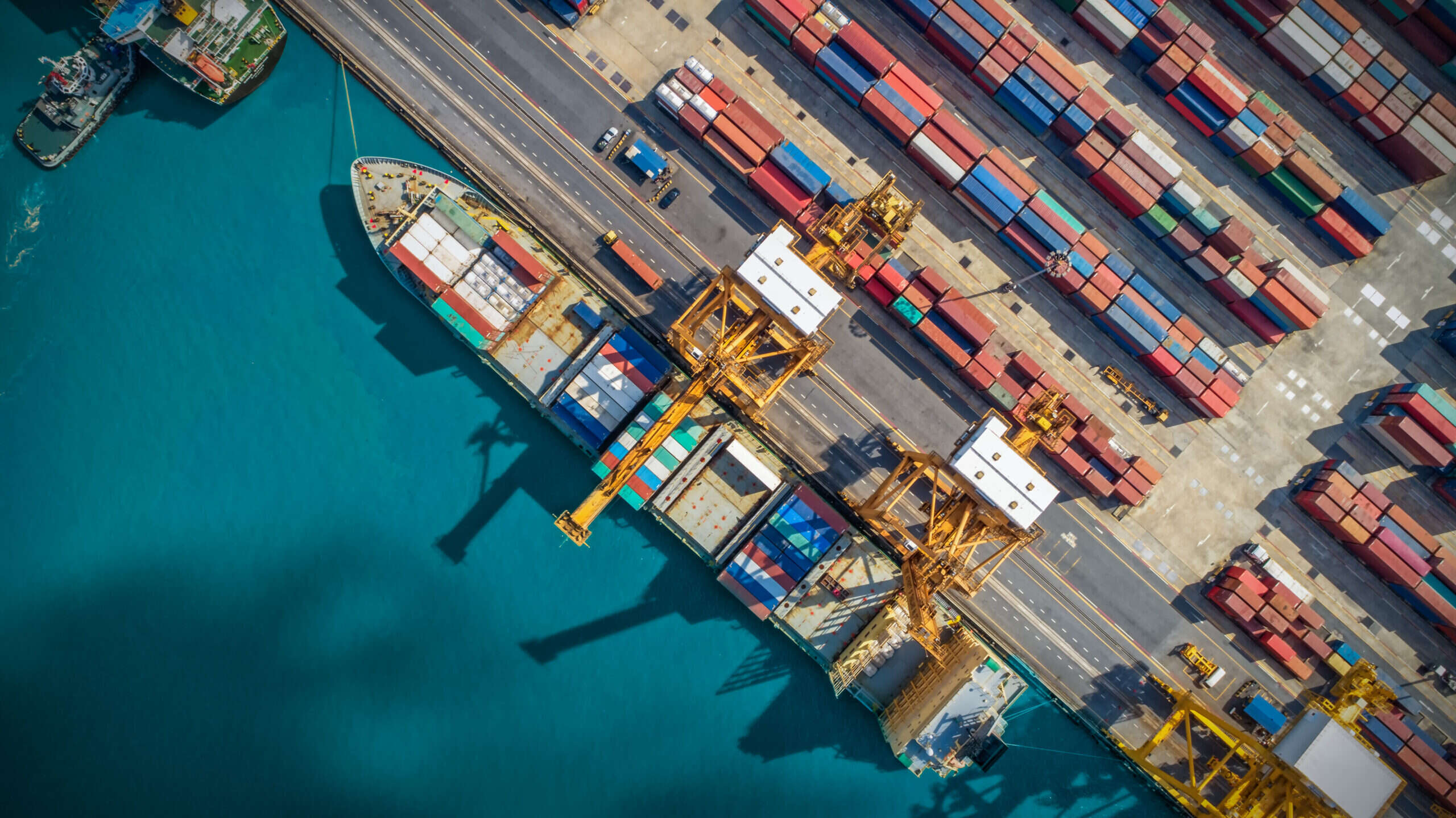
Many sudden sharp shocks to the supply chain – among them Brexit, Covid-19, the war in Ukraine – have not only shown UK manufacturers the limitations of legacy technology platforms, but highlighted the need to be more responsive to a changing risk landscape. Disruption and volatility in global trade has become the norm, and manufacturers may abandon ‘just in time’ practices in favour of more certainty of supply.
In short, the rules of the supply chain are being redrawn, with resiliency rather than efficiency becoming the top priority. Companies are looking to bring their supplier network closer to home, and digital technologies will also play a part in building resilience.

“The supply chain has been massively disrupted,” acknowledges Andrew Kinder, SVP Industry Strategy at Infor. “One of the areas in close focus is visibility up and down the supply chain.
“Things like lean manufacturing and JIT (just-in-time) work perfectly when suppliers deliver efficiently but fall apart very quickly when they don’t,” he adds. “Offshoring works great when there are reliable trade relations between nations, as does single-sourcing when products are in common supply. All these practices that have been foundational to supply chain strategies are now in question.”
A survey conducted by Make UK for Infor, ‘Building Global Resilient Supply Chains’, polled 132 senior decision makers in UK manufacturing, and the results were revealing – not least around how different types of enterprises were facing different scales of challenges.
“There was a notable difference in the size of the companies who report better supply chain visibility versus those who report no visibility or, at best, only have visibility of their customer and their supplier,” says Kinder.
“Larger enterprises have visibility through multiple levels of their supply chain, which gives them an advantage when it comes to anticipation and response to disruption. This is the same survey segment that also reports greater investments in technology to support supply chain strategy. Which begs the question as to how enterprises that do not enjoy such resources can quickly scale up their tech capabilities.”
Legacy systems left behind
A more resilient supply chain is built on three things – greater visibility, connectivity and intelligence. Technology will be vital in helping companies to incorporate these factors as they remap their supply chains.
“There is a recognition that in order to get to the next level, the ERP system is not enough,” Kinder says. “The valuable data that your supply chain depends on is not actually in your system at all. It’s in the systems of customers, suppliers, third-party providers and financers. The way you orchestrate a supply chain network is through data transparency and data interchange between you and your trading partners.
“That’s something legacy systems were not designed for,” he adds. “When we talk about smart manufacturing, what we talk about is connectivity. Many of our customers find that their existing systems just don’t allow their business to change and grow. They’ve outgrown the system and need to move faster.”
Effective monitoring of supply chains, regardless of geography, has become increasingly important and is a key factor in building resilience. A lack of visibility up and down the supply
chain is a major challenge, so manufacturers are recognising the importance of digital technologies in the monitoring processes. The key advantage of investment in supply chain management is a faster response, and 34% of respondents emphasised the need to adapt to change quickly.
“It’s not all about technology”, Kinder acknowledges. “Companies are re-establishing what their supply chain sourcing strategy should be. Everybody wants quality and on-time delivery, but if you favour rapid response, then you need your supply base to be close to home.”
The Make UK survey found, for example, that 42% of manufacturers have increased the proportion of suppliers based in Great Britain, with further reshoring in the pipeline for more than 40% of respondents, driven by a desire for predictability, certainty, and resilience.
Many companies have also increased the number of suppliers they use in order to mitigate the risks of relying on a smaller supply pool. One in five businesses said they now have between 51 and 100 suppliers in their supply chain, while a further 15% say they have between 101 and 200.
Calling on the cloud
One big change shown in the survey is that the appetite for cloud technologies is growing.
“Several years ago, when we introduced Software as a Service (SaaS) for enterprise applications, people were afraid of going to the cloud because they had concerns over security,” Kinder says. “Now, it’s changed and security has become a positive reason why companies adopt SaaS. Millions of dollars are spent by hyperscalers like AWS and others to keep their systems secure. This level of investment in security cannot be matched by any individual manufacturer.”
Infor specialises in developing business cloud software solutions and industrial manufacturing is among its key markets. Its cloud-based industry suites leverage data science, rely on major cloud service providers, and integrate easily into existing systems.
“Visibility, connectivity and intelligence are the three things we can deliver with a cloud-based commerce network and the cloud approach to software that we have developed,” says Infor‘s Kinder.
“Only one in five respondents to the survey have a digital supply chain tracking platform, which was a surprising statistic. Yet 90% said they expect supply chain pressure to continue through the rest of the year.”
“Manufacturers recognise, when they take a deep inward breath, that they need to modernise,” Kinder says. “UK manufacturers are operating in a high-cost environment, so they compete on their pace of innovation, which means embracing new technologies to accelerate product and process innovation.”