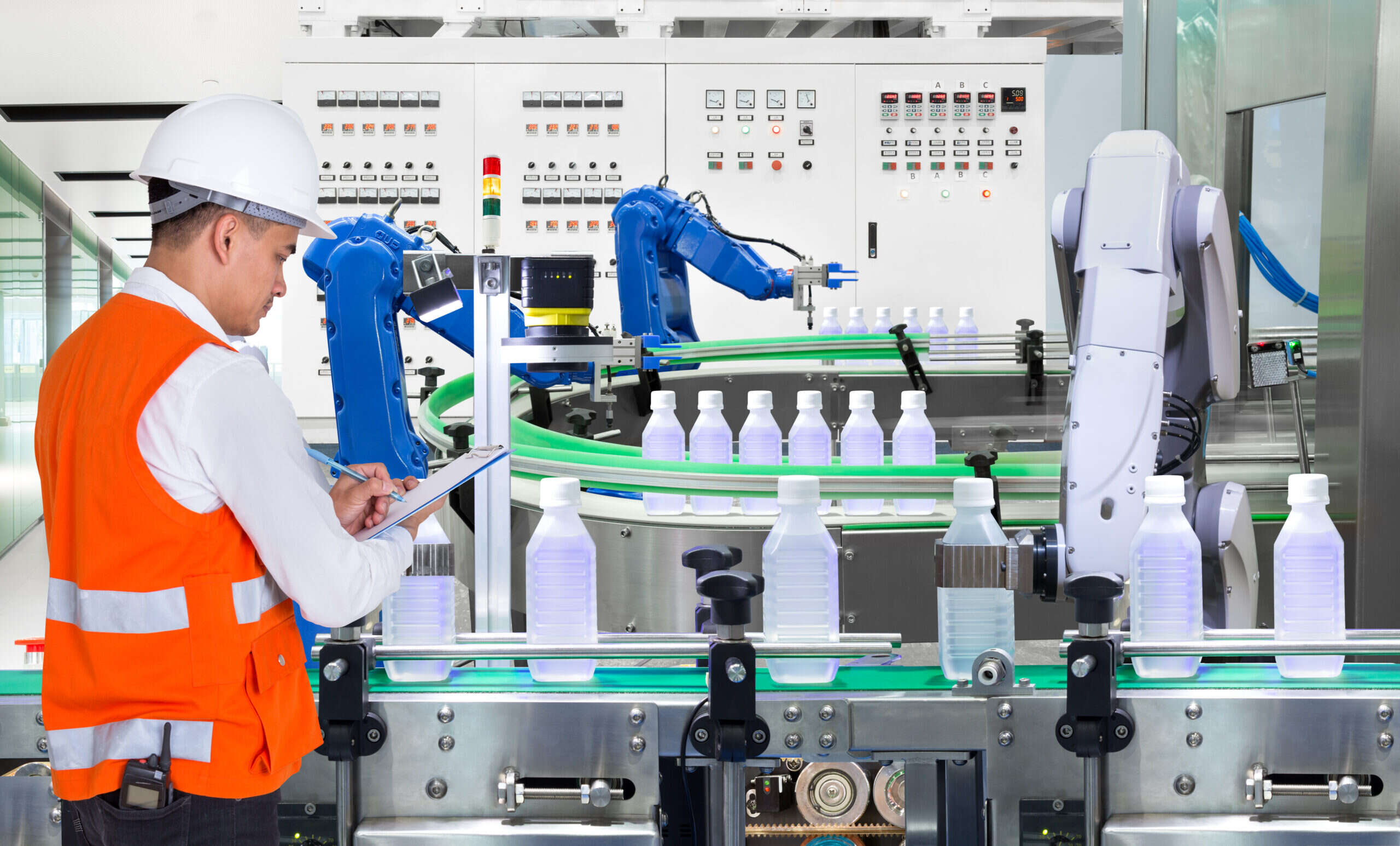
At a time of incredible change and disruption to the supply chain and manufacturing operations, food and beverage manufacturers increasingly require complete enterprise-wide visibility and the agility to respond to ever-shifting market dynamics.
Many of the answers lie in embracing smart technology and automation, but this can be a challenge for an industry not necessarily known for being a frontrunner when it comes to driving digital transformation.

“I would say it’s quite a traditional business with a lot of companies that are not that digitalised yet,” acknowledges Marcel Koks, industry & solution strategy director of food & beverage at Infor. “But things are changing. More companies see they need to invest in automation and the question then becomes how they can do that most successfully and efficiently.”
Koks points to a number of drivers behind this recognition, not least the disruption caused by the pandemic, which accentuated pressures around staffing and operational productivity; time to market; safety and compliance; supply chain resilience; evolving distribution models and consumer behaviour; and growing focus around provenance and sustainability. The energy crisis and inflated cost of ingredients and raw materials is also prompting greater need for operational efficiencies and cost reductions.
Infor offers an enterprise application platform specifically tailored for the F&B sector, with enterprise resource planning (ERP), product lifecycle management (PLM), supply chain and distribution capabilities (SCM) that recognise the unique challenges and opportunities the sector faces. The fact that they are cloud-based removes one of the major stumbling blocks manufacturers face when it comes to pursuing digital transformation.
“Visibility across the enterprise, and the ability to respond to a fast-changing market and demonstrate resilience has never been more important,” Koks concedes. “That’s simply not possible if you’re doing everything on paper and is incredibly challenging if you’re relying on legacy, on-premises infrastructure.”
Moving to the cloud
It is also preventing F&B manufacturers from leveraging the mountains of data upon which they typically sit. In a world of shrinking margins, talent scarcity and rapid digitalisation, embracing cloud solutions in order to embed automation and better analytics into one’s operations is increasingly becoming a no-brainer.
“The equation between cost of labour and cost of capital is changing,” Koks begins. “There is a growing willingness to invest in technology, but a lot of companies are struggling because they are on a legacy platform. There are simply too many technical puzzle pieces for leveraging machine learning, for example, to have all that technology on-site. And every time when one of these puzzle pieces is changed, because the vendor has a new release or whatever, the system breaks down.
“In the cloud, capabilities such as machine learning are available as a service; you don’t have to bother about all the technical puzzle pieces. It also opens up these possibilities to smaller companies, which previously couldn’t dream of accessing such functions. It’s no longer about the need to make huge investment; the challenge is one of education. Many might know machine learning exist, but think it’s about self-driving cars and that kind of thing. We need to explain exactly what it can do for them.”
In the case of ERP, these benefits can include automating food safety processes and increasing regularity of testing; meeting legal and customer requirements through system-directed quality checks and tests; quickly identifying causes of food safety issues and performing accurate, targeted recalls; capturing supply chain and manufacturing data from upstream and downstream processes; and implementing automated corrective actions.
Industry-specific solutions
The Infor executive points to the importance of developing industry-specific use cases in articulating the case for embracing new digital capabilities, evidencing success and allowing peers and competitors to become their strongest ambassadors for digital transformation. This is a process of “continuous innovation”, he says, with functionalities and capabilities developed at the request of one client, potentially benefiting all.
“With on-premises solutions, the vendor installs the software, the client requests customisations, and soon each and every customer has their own unique platform,” Koks explains. “That makes it hard to re-use, share and evolve smart solutions. In the cloud, there is one single version. That means that when we start to build something for a certain client, all clients can leverage the same capabilities. It accelerates functionality and innovation because change is being driven by the entire customer base.”
Digitalisation is already having a tremendous impact on factory production and distribution across the food and beverage manufacturing industry. New tools are enabling businesses to better service the customers, automate decisions, increase food safety, and enhance transparency and sustainability, all at a time of myriad operational and market challenges. But the speed of transformation needs to pick up, with those that fail to utilise the tools at their disposal in danger of failing to remain relevant in such a rapidly changing marketplace.
“As in all industries, there are leaders and laggards,” says Koks. “But we see that digitalised food and beverage manufacturers are managing the disruptions and challenges that the sector faces more successfully. This will only become more evident as the industry becomes ever more data driven. More and more companies are implementing smart technologies and it is driven by more than the need to survive; these capabilities provide the agility and insight to unlock real transformation and innovation.”