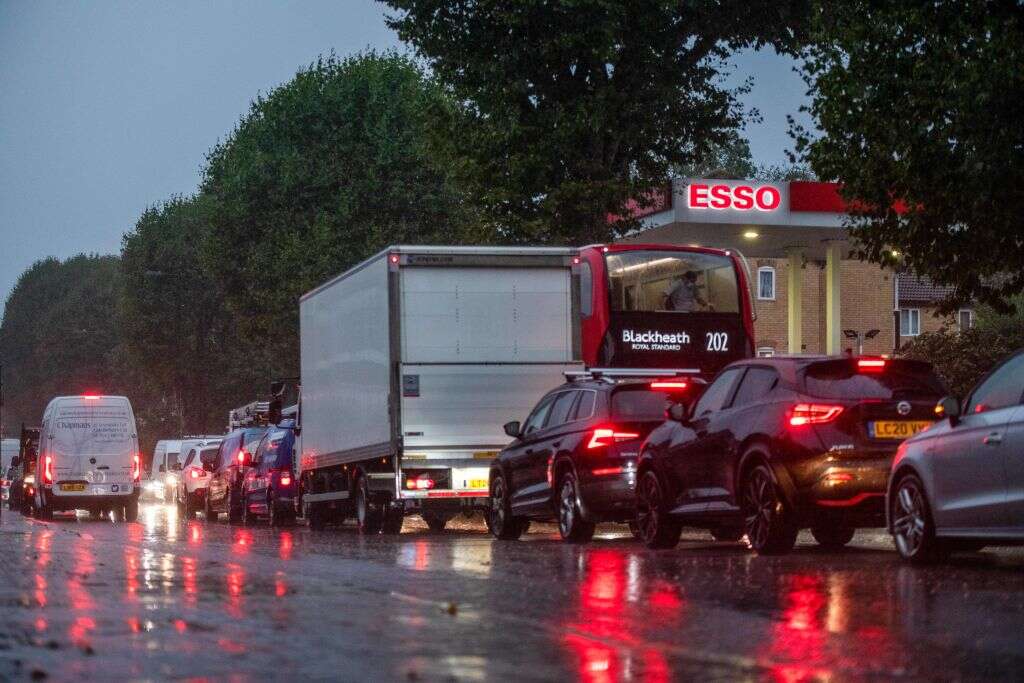
Sometimes, the best way to understand how a system works is to observe how it breaks. The inner workings of the UK’s supply chains are currently on full display: a shortage of heavy-goods vehicle drivers has triggered queues at petrol pumps, while rising fuel prices have sparked a CO2 shortage that threatens the country’s food supply. This, experts warn, is a sign of things to come, as international supply chains are increasingly vulnerable to disruption by geopolitics and climate change. Technology, from AI to blockchain, can help companies understand and diversify their supply chains, but not without collaboration across organisational and national borders.

The UK’s supply chains are in the eye of a perfect storm, with a shortage of HGV drivers causing panic buying of petrol and fuel prices triggering a CO2 shortage. (Photo by Chris J. Ratcliffe/Bloomberg via Getty Images)
What’s causing today’s supply chain disruptions?
The UK’s supply chains are in the eye of a perfect storm. Jens Roehrich, professor of supply chain innovation at the University of Bath, has studied a CO2 shortage back in 2018, tracing its impact to a decision by fast-food chain KFC to switch its logistics provider. The resulting disruption led to shortages of beer, Coca Cola, chicken and frozen food – all of which require CO2 in their production – on supermarket shelves.
The current CO2 shortage is likely to have a similar impact, Roehrich says. “It is highly likely that we will experience problems such as in the summer of 2018 [which] will further increase the likelihood of stockpiling and so increase the issues further. But this time we don’t ‘only’ have the CO2 shortage. We also have Covid-19 and Brexit.”
For seasoned supply chain executives, the current crisis is just the latest of a long sequence of disruptions, says Roehrich. "The last two decades have brought about many disruptions such as the impact of Hurricane Katrina in 2005, the Eyjafjallajokull volcano eruption in 2010, the LA and Long Beach Port strike and the carbon dioxide shortage in 2018, [and] pirate attacks off the coast of Somalia".
Imbalances of supply and demand are often exacerbated by crises such as the pandemic, says Tim Lawrence, director of the Digital Supply Chain Innovation Hub at UK government-backed accelerator Digital Catapult. "The same thing happened after the financial crisis," he says.
Added to this, says Dr Samuel Roscoe, senior lecturer in operations management at the University of Sussex, is growing political intervention in supply chains. This trend began in 2016, with the Brexit referendum and Trump's presidential victory, but has accelerated during the pandemic "People don't think of Covid-19 as a geopolitical disruption but it's not the virus that shut down production facilities or closed borders or shut ports," says Roscoe. "It's governments."
Furthermore, the vulnerability of supply chains to disruption has been increased by 'just-in-time' inventory management, whereby manufacturers stock only as many materials as they need to fulfil their current orders. "This means any small change in demand or supply creates more of a shock," says Lawrence.
Lastly, Lawrence argues, social media has increased the chances of 'demand shocks', such as the current run on UK petrol stations. "One of the biggest demand-side risks is that consumers now have so much more information with which to change their buying decisions."
Reconfiguring supply chains to avoid disruption
Broadly speaking, three overlapping responses help companies improve the resilience of their supply chains. The first is to redistribute them, adding more redundancy and, in many cases, bringing production closer to home. Not only can this reduce the potential for physical or political disruption (although Brexit shows that even close neighbours can have trade disputes), it also allows companies to adjust supply in response to demand.
"If you've got suppliers in Asia and you're sourcing into the UK, you've got six weeks of transportation [in your supply chain], so you can only respond to [shocks] relatively slowly," explains Lawrence. "But if you're closer to your consumers, you can respond more quickly."
This response can be supported by 3D printing, says Roscoe, as it allows companies to move production closer to their customers. "Instead of having sort of big, centralised facilities, you can place 3D printers in various locations around the world that can print customised materials closer to the point of consumption," he explains. "You don't have to worry about port closures, trade barriers or any other government interventions."
Oil and gas giant Shell maintains a 'digital warehouse' containing designs of spare parts for its production machinery. When it needs a replacement part, it will commission a local manufacturer to produce the part, or print it itself. This has led to faster replacement times, the company says, in one case from 16 weeks to two.
Digital technology for supply chain transparency
The second response is to make supply chains more transparent, allowing businesses to detect disruptions sooner or even anticipate them. Traditionally, however, few manufacturers have had visibility into their supply chains beyond their immediate, or 'tier one', vendors, says Lawrence. But the pandemic has prompted many to fix that. Carmakers, for example, didn't pay much attention to who was supplying their component manufacturers' microprocessors until the recent global chip shortage, he says.
But achieving this transparency is "no easy task," Lawrence adds. "Unless there's collaboration between the manufacturer, its tier one suppliers, and their tier two suppliers, they can't find out that information very easily."
French start-up Transparency One is hoping to remedy that by creating a 'social network' for supply chains. Its customers ask their suppliers to input data about their own suppliers, and so on, until a map for each product line is built from the source of the materials to the point of manufacture. This map can then be integrated with, for example, climate or political risk data to assess supply chain risks. During the pandemic, customers were able to integrate Oxford University's Covid-19 government response tracker and anticipate the resulting supply constraints, says CTO Frederic Daniel.
After trying – and failing – to represent this supply chain data using relational databases, Transparency One adopted graph database technology from Neo4J. To understand supply chains, says Daniel, the relationship between nodes is more important than the nodes themselves. "Graph database technology is really designed to manage the relationship between the endpoints, instead of just managing the endpoints."
Supply chain technology: blockchain and digital twins
Blockchain can also help companies achieve supply chain transparency, says Lawrence, by revealing the true provenance of components and their materials. "We've gone through the hype curve [for blockchain] and now we're starting to see some solid use cases being implemented," he says.
"A good example is in the electric battery supply chain. We're starting to see blockchain being used to trace individual batches of materials such as cobalt or nickel, and show their provenance right the way from the mine to the finished product. [Manufacturers] can start to see where risks or supply chain imbalances [are] developing." Earlier this year, mining giant Glencore announced a pilot project with battery maker Umicore, using blockchain to trace cobalt production.
We've gone through the hype curve [for blockchain] and now we're starting to see some solid use cases being implemented.
Tim Lawrence, Digital Catapult
Digital twins are the next step in supply chain transparency, says Lawrence. By feeding real-time data from IoT sensors into digital models of their supply chains, companies will be able to predict the impact of supply chain shocks and test out hypothetical responses. Logistics provider DHL Supply Chain already maintains digital twins of its warehouse operations, as the company's CIO for UK and Ireland Marcus Wuerker told Tech Monitor earlier this year.
It's not just suppliers that disrupt supply chains, however; spikes in demand can cause headaches too. The third approach to supply chain resilience is demand sensing, analysing market data to make short-term predictions in demand. This is an established practice – consumer goods giant Unilever implemented demand sensing software back in 2006 – but advances in AI and the growing availability of data sources are spurring innovation. "We are seeing more and more start-ups and software businesses going into [demand sensing]", says Lawrence. This could pave the way for automated supply chains, where trends in demand feed directly into production without human intervention, he adds.
Supply chain collaboration
The pandemic has provided many companies with the impetus to digitise their supply chains, Lawrence says. Roehrich is hopeful that this innovation will continue. "The current disruptions might also accelerate the progress of more innovative, and hence disruptive, approaches such as additive manufacturing and drone deliveries," he says.
It might also prompt them to manage their supply chains more collaboratively. "Buyers could also think more radically about identifying ways by which [they] can leverage each other’s supply chains, instead of competing with each other," says Roehrich. "In the past, buyers have done this by forming purchasing consortia and combining their material requirements."
Technology adoption primarily happens at big focal firms. But for the smaller suppliers, it's cost-prohibitive and the capabilities just aren't really there.
Dr Samuel Roscoe, University of Sussex
To reap the benefits of supply chain digitisation, large producers may need to invest in uplifting the technology capabilities of their suppliers. "Technology adoption primarily happens at big focal firms," says Roscoe. "But for the smaller suppliers, it's cost-prohibitive and the capabilities just aren't really there. Blockchain is a perfect example: as you get further down the supply chain to the raw material suppliers, people who are mining cobalt in the [Democratic Republic of Congo], what's in it for them?"
A few companies are seeking to address this imbalance, though, Roscoe says. Carmaker Volkswagen, for example, has partnered with blockchain specialist Mine Spider to trace its raw materials back to where they are mined. "They're actually going out [to suppliers] and saying, 'We'll help you do this. We'll buy it, you just have to use it.'"
While the shortages making headlines in the UK may soon be resolved, the need for more resilient supply chains is here to stay. "This is just the beginning of a much longer trend," Roscoe warns. "We're going to see more state intervention in supply chains, whether it's because of Covid-19 or trade pacts. This is the new reality."