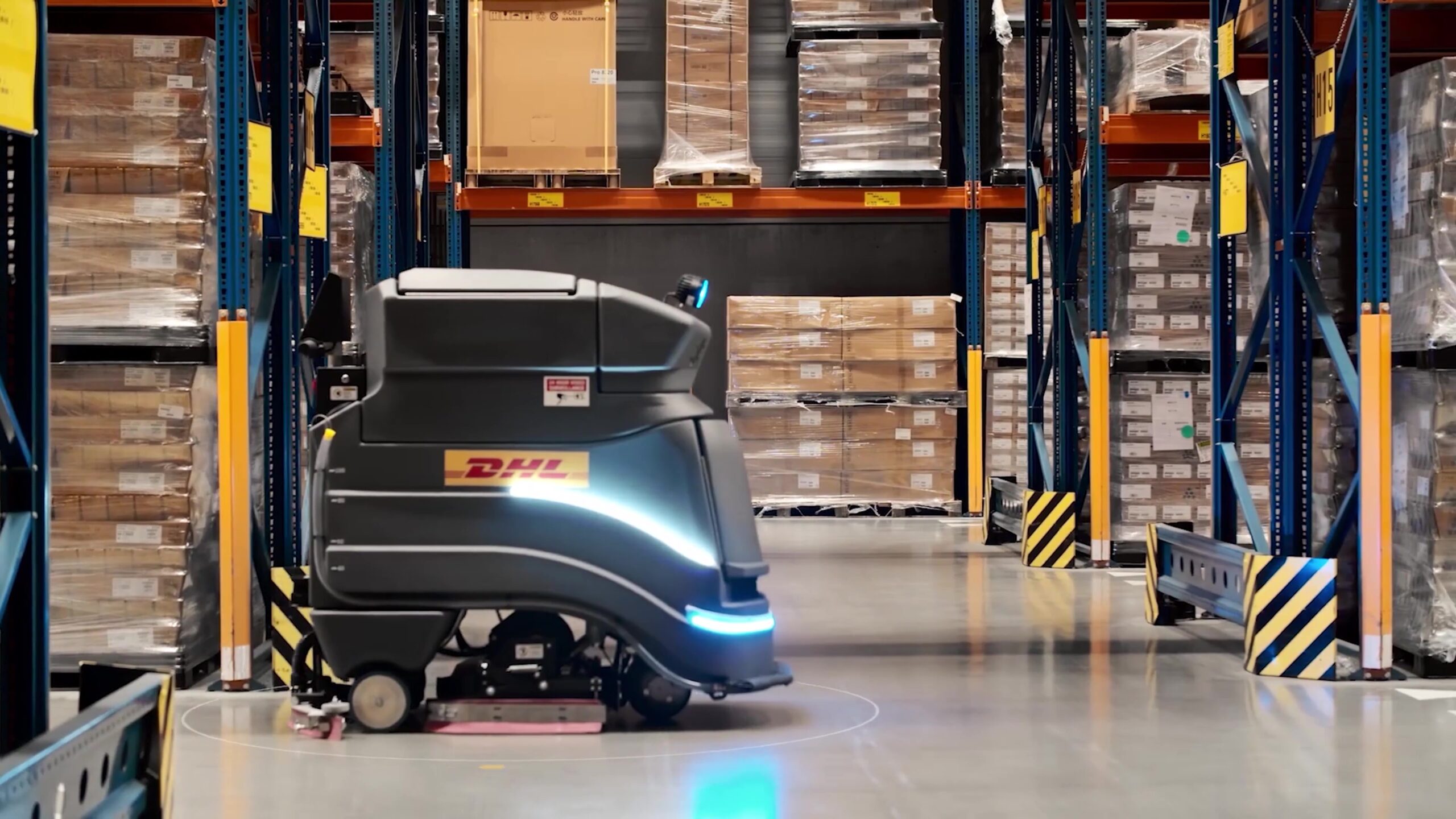
When Covid-19 reshaped the global economy overnight, DHL Supply Chain felt the impact first hand. Some of the industries that it serves, such as automotive, saw demand collapse. Others, such as healthcare, saw it explode. Fortunately for the company, investments in two areas of technology innovation – automation and resource allocation – helped it retool its operations and keep goods moving. Tech Monitor spoke to Marcus Wuerker, CIO for the UK and Ireland, to find out how.

Robotic automation at DHL Supply Chain
The majority of the IT function’s work at DHL Supply Chain concerns “keeping customers happy” by integrating its systems into theirs, Wuerker says. But there are two frontiers of innovation that proved invaluable during the pandemic.
The first is automation – the application of robotics in its warehouse and packing operations. This is born less from a need to reduce headcount than an inability to hire enough workers, Wuerker says. “Our supply chain division employs 165,000 people, so we are a huge employer. But in many markets we just can’t get the people anymore, the labour markets are just [too] constrained. So it’s an economic necessity to start automating activity.”
This includes packing robots, which guide warehouse workers on which items to pick; autonomous vehicles, such as driverless forklift trucks; and ‘cobots’, collaborative robots that work alongside human employees, typically to help pack products with multiple parts such as cameras or advent calendars.
Compared to most industrial automation, developing these cobots is surprisingly agile. DHL Supply Chain buys in the robotic arms, then designs and 3D prints its own grippers for individual assembly lines. “That puts us in a unique place in the market because we can automate without the long engineering time,” explains Wuerker.
We 3D printed an assembly line that has enabled us to kit hundreds of thousands of [Covid-19 tests] a day.
This capability proved its worth when DHL Supply Chain was commissioned to pack the UK’s Covid-19 testing kits. “There are 11 different pieces that need to go into the kit and the country needs 100,000 of these kits a day. And these kits didn’t exist a year ago,” Wuerker says. “We 3D-printed an assembly line that has enabled us to kit hundreds of thousands of them a day.” Once an assembly line is in operation, he adds, embedded sensors track its performance, allowing DHL Supply Chain to optimise and accelerate output.
Resource optimisation for logistics
Meanwhile, DHL Supply Chain has also invested in digitising the way in which employees are allocated. “In a warehouse, we might employ between 50 and 5,000 people. In an e-commerce environment, you might have days where there you have 1,000 orders and days when you have 10,000 orders. So getting the number of people right for the day for the shift is essential for us.” To do so, DHL Supply Chain has developed bespoke systems to predict demand and allocate resources, which it combines with off the shelf time-and-attendance and shift planning software.

Once a staff member is booked in for a shift, the company uses ‘digital twins’ of its warehouse operations in order to decide how best to use their time. “Our digital twins consider all the aspects [of our operations] – incoming orders, the outgoing lorries, the incoming returns – while our systems talk to the customers’ systems, and redirect the workers during the day.”
Unless it is implemented sensitively, this kind of automated management can lead to oppressive and harmful working environments. DHL Supply Chain’s approach is to empower teams to monitor and manage their performance collectively, says Wuerker, which encourages them to share skills. A team might have one member who packs 100 items a day, and another who packs 10. “It’s not about expecting everyone to do 100, because not everyone is a sprinter and it’s not healthy to expect that kind of performance,” he says. “What’s not unhealthy is if you as a team [know] you managed 10,000 order lines a day. That is very rewarding.”
“Don’t strive for 100% perfection, go with 75%”
In March 2020, when demand suddenly shifted between clients, DHL Supply Chain needed an altogether different approach to resource allocation. “We needed to move our people from all over the country into the operations that saw a surge in demand,” Wuerker explains. “We needed to take account of where people live, whether they were willing to travel, and what their contractual constraints were.”
To do this, Wuerker’s team built a “quick and dirty” solution on top of its cloud-based time-and-attendance application that allowed workers to volunteer for shifts that would require a long commute. “We built a resource allocation model that was bespoke for the Covid-19 situation, and went live without any testing,” he recalls. “We turned it on and it worked.”
While DHL Supply Chain’s interactions with clients have returned to normal, this agile approach to development is one of the leadership lessons Wuerker will take away from the experience. “Building a system, not testing and using it for just four months, for one purpose and that purpose only, is something I wouldn’t have done before,” he explains. Now, he says, “I’m much more tolerant of less-than-perfect solutions. Don’t strive for 100% perfection, go with 75%. Try it, improve it, try it again. That is something I wasn’t prone to before the pandemic”.