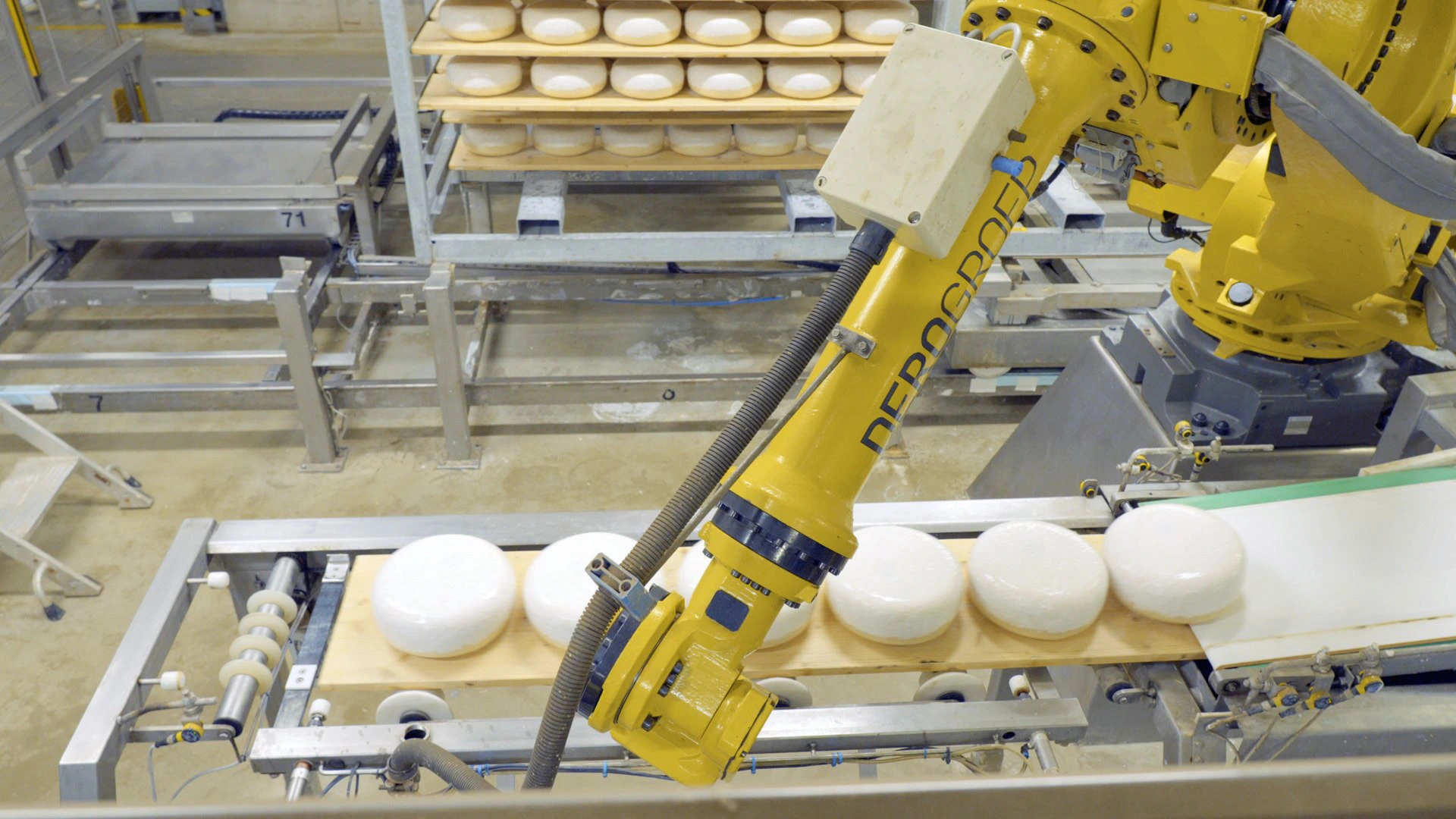
From quality control and food safety to supply chain optimisation and product development, AI and machine learning (ML) technologies offer unprecedented opportunities for efficiency, innovation and sustainability.

More companies in the F&B sector are embracing these technologies to tackle a challenging environment of supply chain disruptions, inflation and evolving customer expectations. This only looks to increase, with the value of the market for AI in the food and beverage (F&B) industry expected to grow from $7bn in 2023 to a staggering $35.42bn by 2028.
Amalthea, a leading goat cheese provider in the Netherlands, is implementing AI and ML into its manufacturing and production operations to improve business and mitigate the issues that F&B producers are facing. With each 1% increase in yield saving the business €500,000, it’s no surprise that improving yield will be a key priority to help Amalthea reinvest savings into innovation and operational business improvements.
Improving cheese yield from milk not only drives profits for Amalthea but also enhances sustainability practices since extracting more product from raw milk reduces waste. As Sandeep Anand, senior director of applied science at Infor suggests, digitising business is a key priority for producers to heed these opportunities, but it begins with the small steps, building out a resilient and efficient process.
Increasing F&B manufacturing capacity using AI
“Amalthea’s long-term goal for digitising started with yield, leveraging data and ML in different stages of the cheese-making process to improve margins,” Anand explains. “The company assessed the different interactions of products and solutions towards yield to help identify discrepancies and quickly readjust and reduce waste. Less waste means more high-quality goods for the customer and more sustainable practices.”
Amalthea sells its products in over 35 countries. As demand for more cheese varieties and products increases, the business aims to significantly increase its manufacturing capacity over the next five years. However, one of the greatest challenges that dairy manufacturing businesses face is the fragility of the product and composition. Without a standard recipe to be applied, consistency cannot be guaranteed, which also presents a risk when capacity is scaled.
To combat this issue, Amalthea identified closer monitoring in the production as a means of rectifying inconsistency issues, maximising yield and maintaining brand reputation while scaling production.
“The business challenge in the cheese industry is that you have a perishable product,” says Anand. “Amalthea sought to find consistent yields for the different recipes of dairy products needed to provide for different customer orders, including goat cheese, cow cheese and the concept of secondary cheese, a combination of multiple cheeses that reuses some of the waste,” he continues.
Understanding deviations to optimise yields
Traditionally, each batch of cheese that Amalthea produced would be measured against a target yield set from historical or practical production knowledge. For any batch that deviated from the target yield, operators would have to adapt and readjust the process in production to increase efficiency. These issues were identified through manual data processing and analysis. Given that around 240,000 litres of milk were processed each day, time delays to implement the necessary changes to improve yield would impact business.
Using Infor’s Coleman AI digital capabilities available with Cloudsuite, Amalthea could solve a critical milk yield business issue that had been challenging due to outdated and disconnected applications, data silos, time limitations and a lack of resources. Different products use varying concentrations of fat and protein beyond the raw materials, many of which are also a variation of locally sourced versus sourced from a further distance. Other parameters such as temperature, product type, raw materials used and respective curdling processes are also closely monitored with data extracted from each. Infor could then process and analyse this data to identify the correlations between these different variables and then apply findings from the output of the yield to optimise future yields.
“Taking a history of different manufactured orders, we built standard template solutions to be used across the milk industry to understand the deviations that are driving the outcomes,” says Anand.
A solution built in just 90 days
“We worked with Amalthea to build this solution in 90 days. It was able to start tracking yield deviations daily, as opposed to a weekly or monthly manual process,” says Anand. “Amalthea was able to pinpoint up to four or five reasons why outcomes might be different. It could correlate recipes with the final output and tie this into a third-party recipe management system where the initial assumptions on these recipes weren’t matching the yield.”
Amalthea could then apply Infor’s Coleman harmonised AI platform to historical cheese batches and orders where the ML model would assess any deviations from the set target yield and draw insights around the yield value daily. This allows for the process parameters of cheesemaking to be regularly updated while adjusting target yield.
A key element of this now fully automated process allows operators to reduce the time spent detecting issues within yield deviations, with the AI technology drawing actionable insights in a much quicker time. This redistributes operators’ time to the stabilising of production processes more efficiently. Infor CloudSuite has also been implemented across Amalthea’s supply chain from milk reception to the cheese warehouse. The system interacts with the factory’s production automation, factoring in weighing units and processing tanks. It also shortens the time to market, which increases speed to value.
Speedier decision-making using AI in F&B
“Amalthea found that some of its biggest drivers of revenue were also some of the biggest drivers of variation in yield, meaning they were leaving money at the table,” says Anand. “Consistent yield minimised this financial loss.”
Amalthea was able to tackle this issue with an initial approach of small, quick wins with tangible, achievable milestones that show monetary or efficiency benefits. As it scaled this technology, the company was able to increase its capabilities of reacting to the process to improve it. Through this continual process, more data and parameters can be analysed to increase the speed of decision-making in a way that wasn’t possible before.
“We were able to connect multiple systems together,” says Anand. “Amalthea had a recipe system, a manufacturing system and a supply chain system. Then you add an analytics view to it as the glue that connects all these different systems together without having to create a completely new system.”
A key benefit of AI is that it helps automate processes and increases efficiency without companies having to build new products on top of it. Amalthea’s use of a cloud-based platform provides a strong foundation for future growth. This use of data insights will become increasingly utilised in F&B.
While it starts with a smaller focus on areas such as yield and production control, automation can be expanded to further use cases to provide more data that can be converted into actionable information. This helps to contribute towards valuable insights that improve performance, allowing for better decision-making and, ultimately, greater profitability.