Dassault Systèmes

Subscribed
You have successfully submitted your enquiry. Someone from our company will respond ASAP
Dassault Systèmes solutions create an unmatched scientific management environment that can help science-based organizations create and connect biological, chemical and material innovations to improve the way we live.
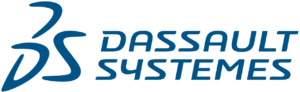
White Papers
How Automated Content Authoring Makes CMC Dossier Creation Easy
Webinar: How Automated Content Authoring Makes CMC Dossier Creation Easy Presented by BIOVIA
Webcast – Unlocking Lab Efficiency
Webcast: Unlocking Lab Efficiency Speakers: Jim Brown, President of Digital Innovation Research, Tech Clarity and Kirsten Gesenberg, Portfolio Director, BIOVIA
The Playbook for Streamlined APQR Generation
In today’s pharmaceutical industry, the practice of structured content authoring is becoming increasingly critical. This approach, which involves organizing content according to specific schemas or templates, is essential for companies as they prepare their Annual Product Quality Reviews (APQR) in compliance with regulatory guidelines. Unlike more conventional, unstructured methods of content creation, structured content ensures a consistent and standardized presentation across all documents, regardless of their complexity or size. Download to find out more.
Controlled Document Management
Document control solutions are essential for the pharmaceutical and biopharmaceutical industries, where they play a critical role in managing drug development, regulatory compliance, and product quality. With the market for these solutions expected to reach USD 44.72 billion by 2030, it's clear that companies need robust systems to streamline document management processes, ensure regulatory compliance, and safeguard patient safety. BIOVIA’s document control solution is specifically designed to support these needs, offering features like workflow management, electronic signatures, and controlled access to documents. Download to find out more.
5 Ways to Digitally Transform the Lab
Chemical labs are critical to every aspect of manufacturing, from R&D through scaleup to operations. While manufacturers have continuously improved product quality and manufacturing productivity through continuous improvement and digital transformation, the lab is often left out of these initiatives. That leaves lab managers with a patchwork of solutions and disjointed processes that burden scientists and technicians with non-value-added work. Poorly integrated lab environments take highly trained lab resources away from innovating and slow down product development, product launch, and product release. It's time to get the most out of the lab through continued digital transformation. We've identified five dimensions to measure and improve lab integration to optimize lab operations and enhance overall business performance. These dimensions include better integration between people, process, and technology in the lab, including integration of systems around a common data model. We'll look at each of the dimensions in detail and discuss how taking a platform approach helps achieve them. Download to find out more.
BIOVIA Biopharma Quality Management Analyst Solutions
The pharmaceutical supply chain faces ongoing challenges, with the FDA issuing over 130 recalls in 2022 due to quality issues exacerbated by the pandemic. Biopharma companies are turning to digital quality management solutions to address compliance and overall product quality. Download to find out how.
Integrated Quality Management System
A biopharmaceutical firm encountered difficulties due to isolated documentation and manual entry errors in their quality management system. To address these issues, they implemented BIOVIA’s Biopharma Quality Management Analyst (BQM), a Software as a Service (SaaS) solution seamlessly integrated with the 3DEXPERIENCE® platform. Learn how with this use case.
Navigating the Complexities of Documents in CMC Dossiers the Power of Structured Documentation
A study published in the Journal of Pharmaceutical Sciences offers a compelling outlook on the future of CMC regulatory submissions. Researchers predict a shift from traditional documentation to structured content and data management (SCDM) for dossiers. This strategic transition is anticipated to significantly streamline the process of CMC regulatory submissions. In this white paper, we will explore the challenges organizations encounter with traditional documents, and how adopting SCDM for CMC authoring can result in substantial benefits across various business operations. Download the white paper to learn more.
Transforming CMC Generation Through Automation and Structured Content
Unlock the potential for unprecedented efficiency and cost savings in pharmaceutical and biotech companies with BIOVIA's Structured Document Manager and the 3DEXPERIENCE® platform. Tackle the challenge of automating the creation of Critical Manufacturing and Control (CMC) dossiers, fostering seamless collaboration, eliminating manual errors, and adhering to high regulatory standards. The solution not only revolutionizes the document creation process but also yields remarkable results, including $2 million in cost savings per dossier, an 80% reduction in time for stability, batch analyses, and specifications sections, and a 50% time reduction in CMC content authoring. Dive into the future of structured content authoring and discover how this innovative approach can transform the way pharmaceutical teams operate, ensuring faster time-to-patient and substantial advancements in productivity and quality. Download the use case to learn more.
Tackling CMC Authoring Challenges
Authoring Chemistry, Manufacturing and Controls (CMC) dossiers is a complex process. Information is collected from the early development to the approval of the Marketing Authorization and beyond once the product is commercialized. Before a medicinal product can reach the wider population of patients, clinical studies take place. This will ensure the safety and efficacy of a product for its intended use. A product used in humans is subject to high scrutiny from the Health Authorities and clinical studies are closely supervised. Biopharmaceutical companies need to provide precise information on the quality of the product. For example: how and where is the drug made, what kind of materials are used and how are they tested, how can the methods used to test the raw materials assure product consistency and quality, how long can the product be used, how have the specific quality attributes been identified and how they are controlled and monitored. Download the white paper to learn more.
Optimizing Production Planning and Scheduling For Maximum Efficiency
A leading Pharmaceutical Manufacturer leverages DELMIA Ortems software to plan, schedule and optimize operations at more than 18 facilities around the world, integrated with a variety of ERP environments. Recognized as a world leader in the pharmaceutical industry as well as in human vaccines, the manufacturer offers an extensive portfolio of pharmaceutical products, including prescription drugs, generics, consumer healthcare and animal health products. It needed to find a better method to manage production in a highly complex manufacturing environment, which includes varied manufacturing modes such as the manufacturing of pills, coated tablets, gels, eye drops, injectables and other products. In order to make up for its ERP's functional shortcomings in finite-capacity planning and scheduling, the manufacturer initiated a process to optimize its manufacturing processes so it can transition from a static to a dynamic planning and scheduling mode with DELMIA Ortems. Download the case study now to read more.
Maximizing Production Throughput – Customer Story
Pacira is an emerging specialty pharmaceutical company headquartered in the US that focuses on the clinical and commercial development of new products that meet the needs of acute care practitioners and their patients. The company’s emphasis is the development of non-opioid products for post-surgical pain control. Pacira has developed a proprietary product delivery technology (DepoFoam®) that encapsulates drugs without altering their molecular structure and then releases them over a desired period of time. This improves products’ efficacy and safety, making a critical difference to patients in terms of dosing frequency and administration. The product EXPAREL® based on this technology is marketed to replace opioids for post-surgical treatments eliminating addiction and overdose deaths. It is manufactured in San Diego, US and Swindon, UK. The production of the emulsion is very difficult to control, involving two emulsion steps: solvent stripping and buffer addition for storage and potency adjustment. To hear more, download the customer story.
Sustainable Pharmaceutical Manufacturing With The Virtual Twin Experience
The growing global demand for pharmaceuticals due to longer, more affluent living, presents many challenges for the industry. While the Life Sciences and Healthcare industry aims to improve the quality of our longer lives, there is a growing recognition that the pharmaceutical sector must do more to improve its sustainability performance. To meet the high demands of sustainability, traditional ways of innovating will not affect manufacturing sustainability quickly or effectively enough. Instead, manufacturers need to leverage the power of the virtual twin to optimize their real-world impact before building their plants and supply network. Virtual twins are a crucial solution to solve complex pharmaceutical manufacturing sustainability challenges, such as achieving zero carbon and integrating more closely with the circular economy.
The Digital Lab is Here
This white paper explains relevant aspects of the Digital Lab - an overall laboratory informatics solution that spans the lab-to-commercialization product lifecycle, using data standardization/ harmonization technology and integrated platform capabilities to streamline technology transfer and support operational excellence initiatives. The paper also addresses the usefulness of a single, unified, scientifically aware environment in accomplishing technology handoffs along the lab-to-plant continuum, and the importance of consistent, standard procedures for managing data and processes from lab to commercialization. Download the white paper to learn more.
Transforming Biopharma Process Development – Use Case
The BIOVIA Unified Lab offers research, development, analytical and QA/QC laboratories a unique opportunity to truly digitalize their lab processes and to connect analytical and process workflows end-to-end. With the Unified Lab from BIOVIA, daily workflows are truly digitalized, non-value added tasks are minimized and organization are able to transform their lab operations. Download this use case now to learn more.
Selecting an Electronic Lab Notebook – 7 Things You Must Know
The right electronic lab notebooks (ELNs) strategy and solution can set your organization above the competition in terms of scientific information capture, workflow optimization, process consistency, IP protection, collaboration within global virtual teams and improved productivity through knowledge sharing. Download the white paper to learn more.
Digital Lab Documentation
Life Sciences organizations need to bring new high-quality therapeutics to market fast to respond to patient needs specific to different diseases and geographies. But development time and costs for new therapeutics are gigantic with an average accrual of $2.6B and 12 years from ideation to market. Reasons for the struggle include (1) the long “time to fail” in new target identification, (2) increasing global and regional regulations and scrutiny, and (3) the major efforts required to ensure that therapeutics are safe, efficacious and compliant with specifications. Personalized Medicine and Patient Centricity add complexity to Development and Manufacturing. Testing is required to confirm therapeutic characteristics discovered during Research, to identify and optimize formulations for production and scale-up, and to release active ingredients and products. Download the White Paper now.
Accelerate Digital Transformation with BIOVIA Scientific Notebook
To accelerate digital transformation, companies are opting for a cloud-based implementation of the Dassault Systèmes 3DEXPERIENCE platform. The first stage is leveraging BIOVIA Scientific Notebook on the 3DEXPERIENCE platform. Experimental data from legacy electronic lab notebooks (ELNs) can be indexed and accessed with Scientific Notebook, making it into a single, centralized database on the platform for all researchers and scientists. Download this use case to see how BIOVIA Scientific Notebook and the 3DEXPERIENCE platform are helping life sciences companies continue their digital transformation journeys.
How To Manage Compliance in a Global Media Device Company
This medical device company develops, manufactures and markets critical customer care products worldwide. To improve the efficiency of company offices, manufacturing facilities and distribution centers around the world, the company approached Dassault Systèmes to assist them in better integrating the common elements of compliance including content, processes, people and systems across the organization. Get the Use Case
The 21st Century Lab
Life Science companies face major challenges to continued operations and profitability from patent expirations, low R&D productivity, increased competition, decreased margins, inefficient processes, and mounting compliance constraints. Get the eBook now