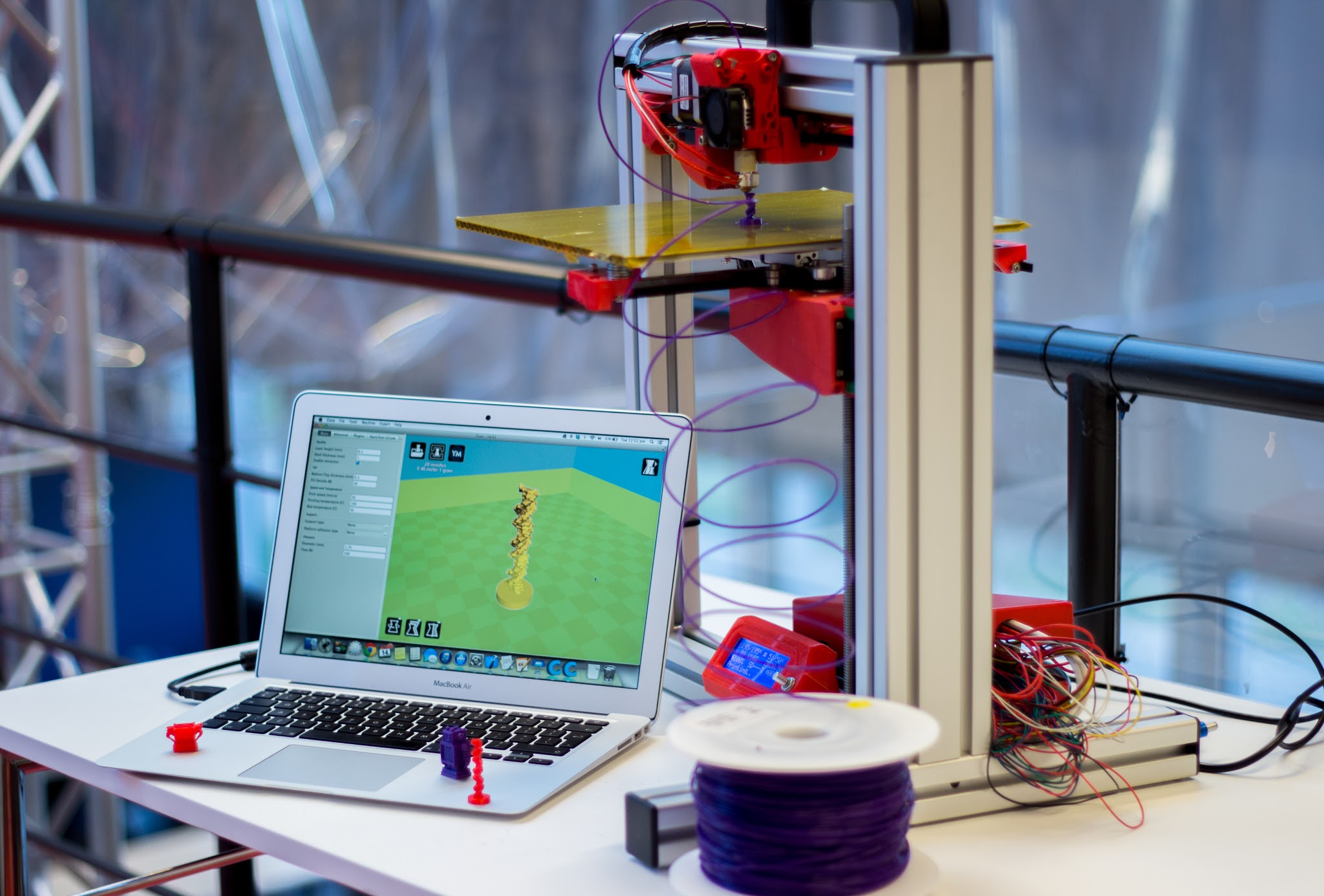
Ford and 3D printing company Stratasys announced that they are going to begin testing 3D manufacturing car parts.
The two companies will be starting a pilot program designed to see if they can cheaply and more effectively use 3D printing to create large parts and components in small scale batches. The hope is that Ford will be able to create parts in smaller volumes when it would otherwise prove too costly to produce them.
In the past 3D printing was limited in its size but Stratasys has developed the Infinite Build method that utilises printer heads and larger industrial robots to create larger parts for cars and other vehicles.
The technology could prove beneficial for vehicle customisation, particularly race cars. Cheaply produced components would allow crews to experiment with prototype parts that could be much more easily manufactured and installed to the vehicle.
A Ford race car previously won the 2015 Rolex 24 at Daytona using a 3D printed intake manifold. The Infinite Build 3D printer will allow the opportunity to increase experiments in a similar vein to this.
Smaller desktop 3D printers work by using a plastic filament that is layered upon itself over time to create a shape from the ground up. The Infinite Build process from Stratasys differs in that its use of industrial robot heads and pellets of plastic, as opposed to a continuous stream, allows the devices to print much more complex shapes and sizes in three dimensions. It should also allow designers to optimise strength and weight through a more detailed design process.
However, Ford does not believe that this is a viable alternative to all manufacturing though it could prove useful in specific cases.
Previously, Local Motors, were able to create an entirely printed body for its electric Strati car which it plans to sell to customers. The Strati however, is a small and simple design so it could be some time before 3D printing can be used for mass automotive production.