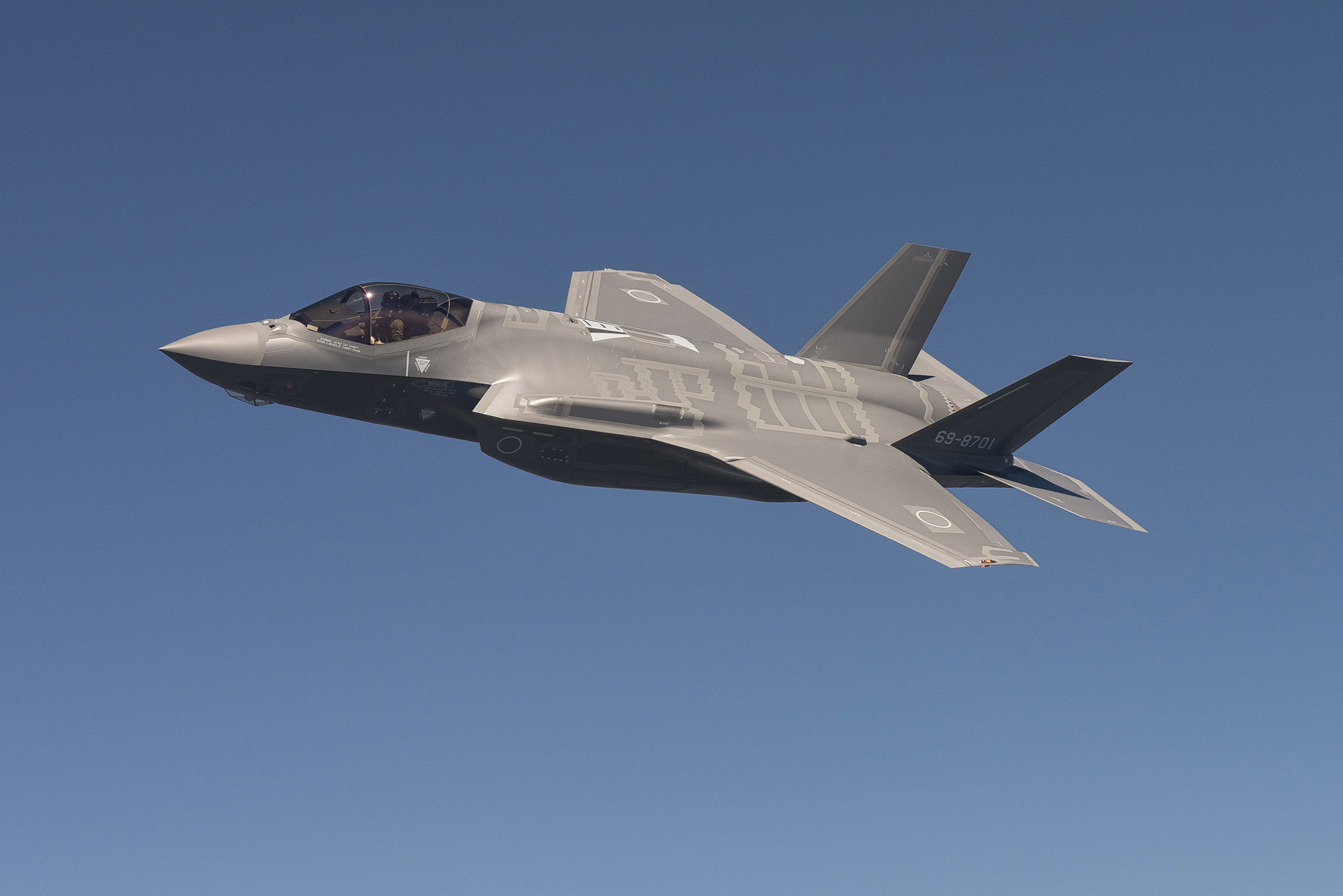
The first thing that grabs you when you enter the F-35 factory is its size: wall-to-wall the production line in this Forth Worth, Texas facility is a mile long.
A central passage stretches into the near-distance: off it, industrial equipment and supports hold F-35 fighter jets in varying stages of construction.
The second thing that hits you is the quiet.
The Lockheed Martin plant in which this $1 trillion-plus, fifth-generation stealth fighter is being built was first constructed during World War 2.
When its first product, the B-24 Liberator heavy bomber, was being built along its production lines, the clamour would have been deafening.
Yet a new generation of jets brings a new generation of industrial equipment: walking the factory’s central thoroughfare you are stepping on concrete poured in the forties.
With the advent of automated drilling and riveting machines, the factory floor had to be re-poured with strengthened concrete. This has resulted in an eerily quiet industrial space; the machines are muted: not once did I hear a drill whine sharply, or the abrupt hiss of compressed air, despite the approximately 7,000 people working in it per shift.
Size and general impression of silence aside, it is a factory like any other: workers mill around moving parts; oversee automated tools; laugh as they eat in cafeterias on the factory floor. It’s just a factory: but a vital one for the US, UK and their allies.
The facility is operated by Lockheed Martin, which is tasked with assembling the world’s most high-profile and high-technology fighter jet.
The F-35 is a weapon that transcends how we typically think of a fighter jet: Lockheed describes it as “designed to be a key net-enabling node in a system of systems – an information gatherer and transmitter in a vast network.” (At its heart is a core processor that can perform more than 400 billion operations per second).
And my overall impression of it as a “normal” factory may have to do with the fact that a great deal of classified work is happening out of sight.
What I didn’t see on my visit: the teams adding the final layer of paint that contains classified ingredients which make the F-35 practically invisible to radar, as it absorbs and reflects radio waves.
Or the laboratory where a completed F-35 is blasted with radio waves to confirm the jet is invisible to radar. (This test is so accurate that when finished, Lockheed has a radar signature that is so highly unique to each jet, that if you were to place a coin on the wing, the defence contractor could tell you if it was heads or tails.)
Then there’s the eight million lines of software code; the stupendously powerful custom processor to handle all the data flowing in and out of the plane. The helmet that lets you see whales underwater… (Read on).

F-35 and the Next Generation
As Steve Over, Lockheed’s director of business development told us: “We’ve taken network enabled operations to the very next level.”
This is most viscerally obvious to a pilot: in the earlier F-16, a dedicated display illuminates targets on a screen in the cockpit. The pilot uses the interface to manually cycle through radar modes, while controlling a thumb wheel on the throttle controls that affect antenna elevation, and handling controls for the electronic warfare system.
“If you’re a fourth generation pilot, most of your mental capacity is consumed by controlling individual sensors and then interpreting what those individual sensors are telling you,” notes Over. The pilot, in short, is trying to manage all of these inputs and controls simultaneously, while flying a fighter jet in potentially hostile airspace.
This is taxing, prone to error, and where what Lockheed calls ‘sensor fusion’ comes in instead: the F-35’s on-board systems and sensors automatically collate all of the incoming data and provide the pilot with a robust 3D visualisation of the battle space.
“The pilot’s not doing it, the computing engine inside the aircraft is managing all this. It’s not just doing it with the radar. It’s doing that with electronic warfare and other infrared sensors,” Lockheed’s Over notes.
The pilot, in short, is now sitting in a weapons platform that is feeding them battlefield information that they have the last action call on.
The ability of the technology to render this vividly for the pilot can’t be understated: the sensors feed data to the much-talked about F-35 helmet, built by UK-based Gentex Helmet Integrated Systems for approximately £350,000 each, with other key contractors involved in its creation including the US’s Rockwell Collins, which developed the helmet-mounted display system
Using this, if the pilot looks down at their feet they won’t see them: instead they will see right through the plane to the ground or ocean below. Cameras and sensors on the jet feed the pilot a 360- degree real-time video; augmented with a huge array of sensors. (For night flying, the night vision view is projected directly onto the visor, cutting out the need for separate night-vision goggles).
Alan Norman is the director of Lockheed’s F-35 flight test programme and served in the US Air Force for 23 years as a fighter pilot and test pilot.
He told Computer Business Review: “If I’m flying over an environment like desert terrain, I’ll see little trails of animals and all kinds of things that I would never see before. If I’m out over the ocean, I see little boat trails cross the ocean that I didn’t see before.”
He adds: “In fact, the very first test we ever really did with DAS (Distributed Aperture System) involved taking it out over the Pacific Ocean.”
“The first pilot that did it was complaining up a storm saying, ‘I’m not sure the system’s working all that well. I’m getting this really fuzzy image of a boat down below me out in the Pacific’. And he goes: ‘Oh, wait. The boat jumped out of the water. It was a whale!’ He was looking at underneath the water with the system.”
Even the way these jets communicate is disrupting the standard.
Currently NATO uses a military tactical data link network know as Link 16.
Steve Over notes that there are issues with this system as: “If you get into a dense combat environments, you get a network going.”
“It’s common that there are too many users on the net and therefore bandwidth is very limited. And the other thing, its omni-directional. Right. So a transmitter that is on the Link 16 network is beckoning as it’s airborne in the sky and it’s transmitting in all directions, which makes you vulnerable to adversaries that are listening for links, extreme transmitters, but it also makes you vulnerable to adversaries that try to jam your net.”
To get around this issue the F-35 has a Multifunction Advanced Data Link built in as standard. This link establishes narrow directional communication and allows the stealth jets to communicate without giving away their position or vital intel.
The UK’s Involvement in the Project
Walking around the facility and seeing the Star Spangled Banner and bald eagle everywhere you would be forgiven for thinking that the F-35 is solely an American creation.
The UK in particular has been central to the project’s development: BAE Systems holds a 13-15 percent workshare of each aircraft, excluding propulsion, and at peak production, estimates that the programme will be worth some £1 billion to UK industry alone, with an estimated 25,000 UK jobs sustained across more than 500 companies in the supply chain.
HMG is expected to purchase 138 F-35s in the coming years and as of July this year has received its eighteenth jet, which was flown to an RAF base in Marham Norfolk.
British companies are heavily involved in the manufacturing process of the F-35, especially the B variant of the jet. Rolls-Royce is responsible for the jet propulsion system and the B’s one-of-a-kind vertical lift system: the short take-off and vertical landing (STOVL) engine lets the jet essentially float stationary in the air at the flick of a switch.
BAE Systems has provided the Aft Fuselage and structural components. Honeywell Aerospace has developed the life support system, while GE Aviation’s UK operated factories have done work on the electrical power management system and the fuselage remote interface units.
As with any hugely high capex military project like this, issues remain: while cost-per-plane is falling to close to $80 million, reports suggest providers along the supply chain are still struggling to get parts to the Lockheed production line on time.
The US’s Vice Admiral Mat Winter, the F-35 programme executive told lawmakers in May: “I’m hitting a stagnant plateau with Lockheed Martin because they are 600 parts behind on average: 600 parts not on the production line when I need them,” he said.
The company says it is making progress however, and has flagged its integration of an Automatic Ground Collision Avoidance System (Auto-GCAS) into the planes seven years earlier than previously planned.
“The F-35 is the most survivable fighter jet in the world today – and the addition of Auto-GCAS will further enhance safety and save lives,” says Greg Ulmer, Lockheed Martin’s vice president and general manager of the F-35 program.
And as a commercial project it looks set to not just survive, but thrive for some time yet: sixth generation fighter jets are not expected until the 2030s and 2040s, and for the UK, it will be operating alongside the Typhoon to carry out air-to-surface, electronic warfare, intelligence gathering and air-to-air simultaneously; quite a mix of capabilities.
See Also: On Copehill Down, a Technology-Augmented Army Gathers