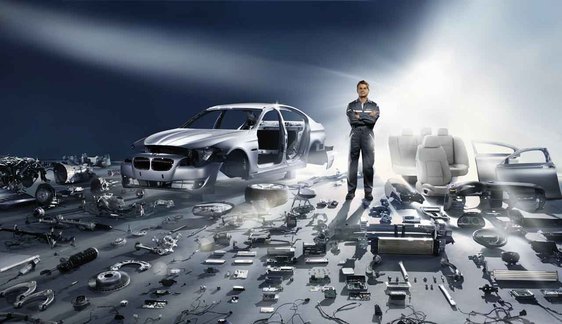
BMW, one of the largest car manufacturers in the world has turned to Teradata to manage its increasingly complex supply chain.
Operating in 31 production and assembly facilities in 14 countries and a global sales network in more than 140 countries and a growing demand to be customer-oriented, the BMW Group, which includes BMW, MINI, and Rolls Royce, is faced with producing more vehicles in local markets and managing a global supply chain network.
Adding to that complexity are the numerous logistics service providers that the Material Control Overseas Plant department of the Group partners with in order to ensure that the supply of parts to these plants is in-time and cost effective.
The Group is faced with tracking the journey of a single part through the whole of its overseas supply chain, something that may see it moving from where it was manufactured, on to BMW Germany, then on to another supplier that might use it to manufacture a part of the car.
Thousands of parts are moving through the system at any one point in time and it was faced with difficulties in alerting overseas plants when there were delivery bottlenecks. To combat this the Group would express ship the parts at great expense, something that also made it difficult for BMW to accurately identify costs and cost drivers.
The car manufacturer had been using tools like Microsoft Excel, Microsoft Access, and SAP Business Information Warehouse to analyse the data along the supply chain, but Stefan Betz from the Material Control Overseas Plants department of BMW Group, said: “Our traditional instruments increasingly reached their limits.”
This convinced the Group that it needed a system that would be able to deal with the increasing amounts of big data generated by the supply chain and a deeper and timely analysis of this data. So it started a new project with the aim of achieving transparency across the whole of its supply chain to BMW overseas plants.
The Group decided to introduce Teradata’s Agile Information Platform (AIP) and made the company its technology and implementation partner.
Betz said: “The need for maximum transparency across all the important supply chain processes was ultimately the main reason we decided to introduce the Agile
Information Platform.”
During the implementation, the team at BMW used the tech company’s logical data model for the transport and logistics sector, which meant that the team could jump-start the creation of their data warehouse, and create a blueprint for the AIP’s data architecture.
The AIP’s data architecture is designed to allow the team to run reports on the data from the supply chain and also analyse this supply chain data with other data sources from around the organisation.
Some of these data sources currently include; inventory, reason codes for air freight, master data, tracking and tracing, programme planning – up to 80 in total.
“Thanks to the AIP, we now have a convenient possibility to bring together countless interfaces and large amounts of data. We can, for example, analyse where stocks are too high or transports are underutilised,” said Betz.
The technology provides a platform that different departments can use to analyse all the data sources from around the organisation on an ad-hoc basis. BMW currently has 20 “power users” for the system and in order to facilitate the analysis of the supply chain some standard reports have been created. Users can also create their own reports to analyse the end-to-end process.
The firms battling to be a standard in big data
Taking control of the project management was the Material Control Overseas Plants department, but they didn’t work alone.
The department also worked with IT, purchasing, and with people from the BMW IT Research Centre at the Clemson University Greenville in South Carolina. This helped to create an overarching committee that could steer the project so that it would reach the best outcome.
BMW says that since the introduction of the AIP it has noticed a greater efficiency in material control thanks to all service providers now being tracked centrally. The result of this is that the material control team can reduce the supply cost as well as executing new requirements faster.
Betz said: “We can now identify deviations such as delayed shipments at a very early stage, so that both the service provider and we at BMW Group can take appropriate action soon.
“This reduce the staff cost and financial expenditure considerably, and it creates room for further process improvements.”

Examples of where improvements are being made can be found in the air freight operation. While it is often the quickest way of getting parts to overseas plants, it is also one of the more expensive forms of transportation.
By analysing inventory, customer order data and other data sources, the BMW team were able to gain better insights into which parts are needed and at which overseas plants. The result of this is that BMW was able to reduce the cost of air freight to its overseas plants in China by almost 70% over two years.
Now that the Group has started seeing success it is planning to add new interfaces and roll out the system to more “power users” and self-service users, one benefit of which is that it removes some of the pressure on the IT department.
BMW also aims to add more data sources to the AIP, such as those from suppliers, and the roll out of more predictive analytics across the business is being looked at.