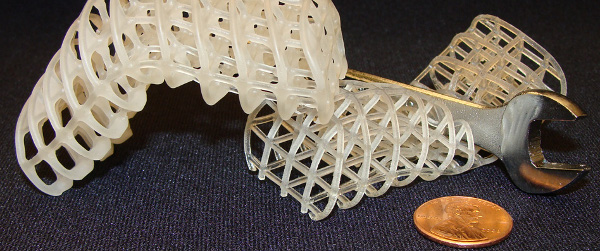
A phase-changing material built from wax and foam, and capable of switching between hard and soft states, could allow even low-cost robots to perform the same feat.
In the movie, Terminator 2, the shape-shifting T-1000 robot morphs into a liquid state to squeeze through tight spaces or to repair itself when harmed.
This new, real-life material could be used to build deformable surgical robots. The robots could move through the body to reach a particular point without damaging any of the organs or vessels along the way.
Robots built from the material – developed by Anette Hosoi, a professor of mechanical engineering and applied mathematics at MIT, and her former graduate student Nadia Cheng, alongside researchers at the Max Planck Institute for Dynamics and Self-Organization and Stony Brook University – could also be used in search-and-rescue operations to squeeze through rubble looking for survivors, Hosoi said.
Working with robotics company Boston Dynamics, the researchers began developing the material as part of the Chemical Robots programme of the Defense Advanced Research Projects Agency (DARPA). The agency was interested in ‘squishy’ robots capable of squeezing through tight spaces and then expanding again to move around a given area, Hosoi said — rather like octopuses do.
But if a robot is going to perform meaningful tasks, it needs to be able to exert a reasonable amount of force on its surroundings, she explained.
"You can’t just create a bowl of Jell-O, because if the Jell-O has to manipulate an object, it would simply deform without applying significant pressure to the thing it was trying to move."
Also, controlling a very soft structure is extremely difficult. It is much harder to predict how the material will move, and what shapes it will form, than it is with a rigid robot.
So the researchers decided that the only way to build a deformable robot would be to develop a material that can switch between a soft and hard state.
Hosoi added: "If you’re trying to squeeze under a door, for example, you should opt for a soft state, but if you want to pick up a hammer or open a window, you need at least part of the machine to be rigid."