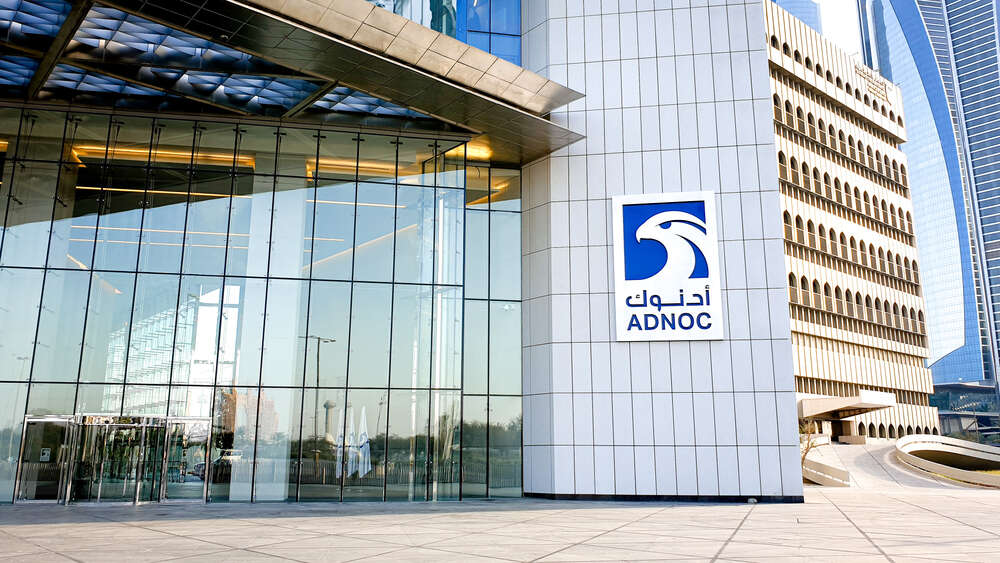
Covid-19 was not the only reason why 2020 was a turbulent year for the oil and gas industry. A price war between Russia and Saudi Arabia after the collapse of the OPEC+ agreement, growing concerns for the devastating effects of carbon fuel on the environment, and the US election of President Biden, whose policies are overtly hostile to oil and gas, have led some to describe it as one of the industry’s “worst years”.
In the UAE, state-owned Abu Dhabi National Oil Company (ADNOC), the largest producer in the country, was no exception to this disruption. But prior investments in a high-tech intelligence centre allowed the company to model the impact of various pandemic scenarios and plan accordingly, while digital innovation on site has allowed it to minimise the risk of disruption due to the disease itself.

ADNOC digital twin: what is the Panorama Digital Command Centre?
Like other oil companies around the world, lockdowns were not the only disruption that ADNOC encountered last year. Unpredictable demand led to rapid fluctuation in market prices, with some products changing price up to six times a day, explains Khaled Al Blooshi, VP of digital projects and innovation at ADNOC. While kerosene and fuel went down due to lack of demand, other products peaked.
Fortunately for ADNOC, the company had laid the groundwork to deal with extreme market conditions back in 2017, when it established its Panorama Digital Command Centre. The centre is a hub that aggregates and analyses real-time information from across the group’s 14 subsidiary companies using big data analytics, artificial intelligence and other advanced techniques. According to the company, it is the only platform of its kind in the oil and gas sector and generated more than $1bn in business value from its inception up to 2020.
Staff at Panorama can simulate ADNOC’s entire value chain – from its wells to customer delivery – and test scenarios to inform the decision-making process, explains Al Blooshi, who led the centre’s development. For example, the system can predict the sales impact of reduced capacity in one of its resid catalytic crackers, a key component of the refinery process.
“When we built this entire digital twin of the value chain and we have access to the real-time data, this helped us to run the simulations with a couple of clicks,” says Al Blooshi. “Within ten minutes or one-hour maximum, you build the model, you adjust the model and you give it an instruction of what you need to optimise. Each scenario runs in the background doing thousands of calculations until it tells you what’s the best production plan to reach this output.”
This scenario-modelling capability proved invaluable in the early stages of the pandemic, when its impact was impossible to predict. “We had scenarios on the model where we had to shut down the site,” he says. “We were prepared for that scenario if, God forbid, things got worse and reached that situation. How are we going to fulfil market demand and customer needs? We were ready because we had run all these scenarios and had business continuity plans prepared for [the] worst situations.”
We were ready because we had run all these scenarios and had business continuity plans prepared for the worst situations.
The ability to model the spread of the virus and its impact on operations proved especially valuable, say Al Blooshi. “This model takes into consideration the quarantine period, and how effective are the measures that we are introducing, either social or technical, to isolate people,” explains Al Blooshi. This modelling fed back into the company’s pandemic response. “We were constantly giving feedback to HQ. For example, ‘the measures are not yet effective in site x, maybe we need to go for more rigorous measures’. We then adjusted dynamically.”
Pandemic intelligence powered by the ADNOC digital twin
In February 2020, ADNOC underwent a total shutdown in its refinery, meaning that anyone who was not already on site could not be let in. This meant various vendors and experts who are critical to ADNOC’s operations were denied entry.
Al Blooshi, therefore, introduced remote assistant technology that allowed these experts to advise on-site staff. “All these experts were sitting remotely and advising, doing annotations on the iPads, and telling them [staff on the site] what they needed to do, which buttons they need to click as if they were physically available on the site,” he explains.
ADNOC is also using technology to minimise the risk of infection among employees. The company has issued smart helmets that monitor employees’ body temperature, removing the need for manual tests. It is now rolling out a “smart CCTV” system that uses computer vision to monitor PPE compliance and social distancing. This system was already in development before the pandemic, explains Al Blooshi, to help monitor security in “restricted zones” where there are hazardous chemicals.
This represents a considerable degree of employee monitoring, but Al Blooshi says he didn’t encounter concerns among workers. “We were taking this into consideration: how do we make sure that we are not going into a blame culture? This is very critical for us,” he says.
“Sometimes we have to mask this data so only the people with the right governance have access to this information,” he adds. “We were not interested in knowing [who] the people [were], we were more interested to know if there is an abnormal behaviour.”
Al Blooshi expects many of these measures to remain after the pandemic has subsided. Indeed, as for many organisations, he says: “Covid has helped us to accelerate our digital transformation agenda.”