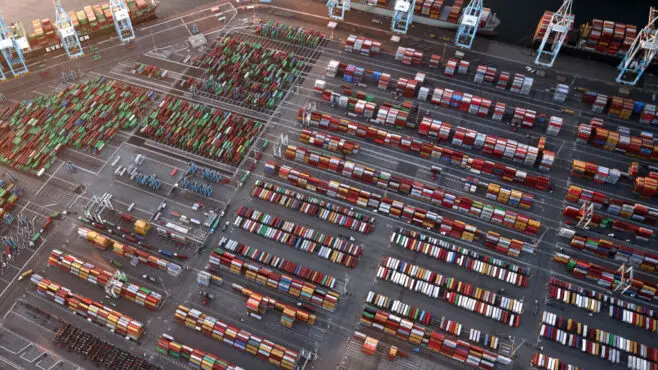
If you want to build a house, you’ll need a truss plate. Looking like the combination of a steampunk spider’s web and a miniature bed of nails, these plates are used to secure the meeting points between timber joints. Able to reduce the tendency of the wood to split under pressure, truss plates have become a vital and overlooked component in modern housebuilding. And this summer, they were almost impossible to source in the United States.
“You couldn’t get trusses,” lumber trader Stinson Dean recently told the hosts of Bloomberg’s Odd Lots podcast. This meant that houses which needed the plates couldn’t be finished, incurring delays on projects further down the line. Meanwhile, the lumber reserved for those unbuilt houses continued to sit in warehouses as more timber arrived to meet demand for orders made before the shortage. The result was a price crash. Perhaps unsurprisingly, Dean is now spending more of his time worrying about the expeditious flow of building equipment. “I’m looking at supply data…talking to my customers about what they’re hearing on lead times on trusses,” he said. “But, [I] didn’t see that one coming.”
Global supply chains have been full of similarly unpleasant surprises lately. Since March 2020, the logistics sector has struggled to cater for a massive (and initially unexpected) increase in demand for consumer goods. The result has been a whole host of shortages in everything from automobile parts and magnesium to books and fake tan. “You can imagine it from kind of a fluid dynamics perspective,” says Chris Rogers, an economist at digital freight forwarding company Flexport. “The pipe hasn’t gotten any bigger, but you’re trying to ram more stuff through it. So, it’s not a surprise that you suddenly run into things backing up.”
Market anxieties have also played their part. “Inventory carrying cost is the second-highest cost after trucking,” says Armstrong, which means that few companies along the supply chain want to handle more goods than absolutely necessary. The sector was left additionally exposed when it made a collective bet at the start of the pandemic that spending on consumer goods would crash while economies locked down. When demand actually rose and retailers rushed to stock anew, shipping companies and freight forwarders struggled to cope, initiating a volatile cycle of stockpiling and ordering known colloquially as the ‘bullwhip effect.’
Consequently, the crisis has also exposed a crucial lack of visibility on the movement of goods across large parts of the supply chain, an opacity that compromises the ability of retailers to anticipate shortages and plan their orders accordingly. As a result, logistics companies are now rushing to invest in new systems that provide them with an overview of where goods are and what obstacles they’re likely to run into as they’re moved from the factory to the consumer.
That has been accompanied by a wider industry recognition that further efficiencies may be required. “It’s not just about the digitisation of the freight forwarding system,” says Rogers, whose employers have directly profited from sector-wide interest in its tracking and analytics services. “It’s about automation across the whole industry,” from warehouses and trucking, to the ports themselves – the hope being that it will help tame the current volatility and unpredictability in supply chains, and help anticipate the next crisis in logistics.

Global supply chains have faced stormy conditions since the start of the pandemic, unable to cope with high – and unexpected – levels of demand for consumer goods. (Photo by Aris Messinis / AFP via Getty Images)
Demand and supply
The term ‘supply chain’ is, in many ways, misleading. Instead of a strong set of linkages between several key stakeholders, the reality of getting goods from A to B is more like a relay race. Take the device you’re reading this article on. Once assembled, that laptop or mobile phone has to be transported in the back of a truck from its factory to a warehouse, and then to a seaport. After waiting for a while in a customs facility, the item is loaded into a container, which is lifted carefully onto a ship, before being unloaded at another port, sent to another warehouse, and arriving at your local electronics shop (providing, of course, that you didn’t order it online.)
“That involves a lot of different companies – at least a dozen, and sometimes more than that,” says Rogers. A supply chain that runs smoothly is one where these firms are in constant and detailed communication about their responsibilities and the constraints they face as they move goods along their small link in the wider chain. And, for the most part, they do, albeit through systems that rely in large part on ageing software, good relationships and well-timed phone calls, emails and faxes. It’s a chain that’s more vulnerable to human error than most.
The fragmentary relationship between suppliers, shippers and freight forwarders “causes friction,” says Evan Armstrong, president of logistics research firm Armstrong & Associates. Mistakes like repeat purchase orders can reverberate “through the manufacturing process, transportation from the manufacturer to the port, through the outbound ocean shipment, all the way inbound to customs.”
As a result, companies up and down the supply chain have begun to invest heavily in digital technologies that preserve flexibility and protect – to some extent, at least – from exogenous shocks. According to a recent survey by DP World, 83% of companies surveyed are now in the process of reconfiguring their supply chains, with most identifying the enhancement of their ‘responsiveness to changes through real-time/predictive data analytics’ as a key priority.
The ideal many logistics firms have begun to reach for, says Armstrong, is known as the ‘control tower’ approach: a central hub where location data from containers, lorries and ships is combined with predictive analytics software to paint a picture of where, when and how goods are moving around the world and what’s stopping them from moving faster. What’s more, it’s getting less expensive to install a working tracking operation, says Armstrong.
Other investments in automation are much more literal. Labour shortages across the logistics sector has made it “hard to meet all the demand that we currently have with manual processes,” says Armstrong. As a result, “you’re seeing things like robots in warehousing operations,” as well as greater interest in digital freight matching.
Even so, new data suggest that not all of these investments are proving effective. A recent survey of freight forwarding companies saw 62% report that investments in automation and analytics were not delivering results as intended, or were not working at all. Then there’s the cost. “Tech debt is a very real issue, not just in logistics but across many industries,” says Rogers. For executives at freight forwarding companies, it’s difficult to justify investing millions in updating tracking and analytics software when the programs that are currently installed don’t break down that often. “All you’re going to see there is dollar signs,” adds Rogers.
The reality is that global supply chains are not run just by a combination of UPS, DHL and Maersk. Logistics as we know it is populated by at least thousands of small companies on the freight forwarding side alone. “If you look at trucking, there are thousands of companies,” says Rogers. “There’s a few big warehouse owners, but there’s thousands of operators.”
The focus of many of these smaller firms, adds the economist, concentrates much more on immediate profitability. Even for those that can boast a turnover of some $25-$30m, says Rogers, “spending $10m on a full digital transformation is a huge deal. And for some companies, that might not even be possible.”
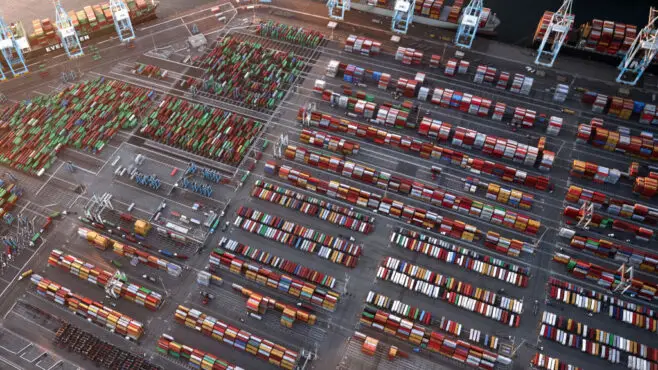
Would digital technology have prevented the supply chain crisis?
If global supply chains had been uniformly outfitted with the latest tracking technology and predictive analytics, would the current crisis have been averted? Rogers thinks not. “Having a whiz-bang, state-of-the-art digital logistics platform isn’t going to change the fact that you’ve got loads of new customers,” he says. “But we would have avoided some of the kind of situations of capacity not being fully used.”
This is particularly relevant for those looking to move goods by sea. An individual supply chain with complete transparency would, says Rogers, facilitate ‘less-than’ container load services and allow companies to spread their consignment of goods across several shipments instead of... all on a single one. This, in turn, would contribute toward easing backlogs and afford retailers greater flexibility in meeting consumer demand. Then there’s communication.
“Imagine using API-based messaging rather than trying to send emails backward and forward, and having somebody remember to type in something somewhere,” says Rogers. Systematising orders and checks would avoid the predictable snarl-ups that arise when any given official down the length of the supply chain forgets to dot an ‘I’ or cross a ‘T’ in a fax. “More standardisation helps everybody,” says Rogers.
This is something that all sections of the supply chain are beginning to realise, according to Armstrong. “It’s somewhat of an arms race, because technology has changed so fast,” he says. “And if you’re not investing in innovation and technology, then you’re going to fall behind.”
Post-pandemic, the results could be dramatic. “What we will see, once we get out of this pinch, is better on-time performance in terms of pick-ups and deliveries, improved inventory management and also better carrier management on behalf of third-party logistics providers,” explains Armstrong. In addition to the normalisation of demand patterns, this should help global supply chains “get back to more of an equilibrium.”
The question remains, however, whether there’ll be enough people able to run all these new systems. The pandemic has also highlighted an issue not discussed enough in logistics circles: a digital skills gap.
“Labour is now calling the shots,” says Professor Nada Sanders, an expert in logistics at Northeastern University. Global supply chain disruption has only highlighted the vital role that truck drivers, port workers and warehouse staff play in keeping our economy moving. Organised labour seems to have realised this, with successful campaigns for pay rises and better working conditions for logistics staff being mounted around the world.
Sanders believes that upskilling should be part of that enhanced compensation package. “And the corporate sector would be wise to offer [it],” she says. “One of the reasons we have this massive labour shortage is not only because we have seen this exodus of the workforce from menial jobs, but we saw early retirements.”
Trucking is one example. “People who plan to leave in their sixties are… leaving in their fifties,” says Sanders. “But people who are in their twenties, thirties and forties do not have the luxury of leaving.”
Indeed, this subject looks to be high on the agenda for ongoing contract renegotiation talks between the Pacific Maritime Association and the International Longshore and Warehouse Union (ILWU.) Failure to conclude an agreement for the 15,000 West Coast dockworkers before the expiration of their contracts next summer could inflict new chaos on supply chains across the US and beyond. The union has historically taken a dim view of automation at the ports, opposing a new automated terminal in San Pedro Bay, California.
Any effort to modernise supply chains with digital and robotic technologies will ultimately have to contend with the welfare of the staff operating these new systems. “Going digital is a key element for companies to avert and prepare for the next pandemic,” says Sanders, “but a part of it is to offer reskilling for labour to make sure that these people are [trained] in two years.” Failure to do so is likely to provoke a new set of crises – one that can only exacerbate the ongoing volatility in global supply chains.