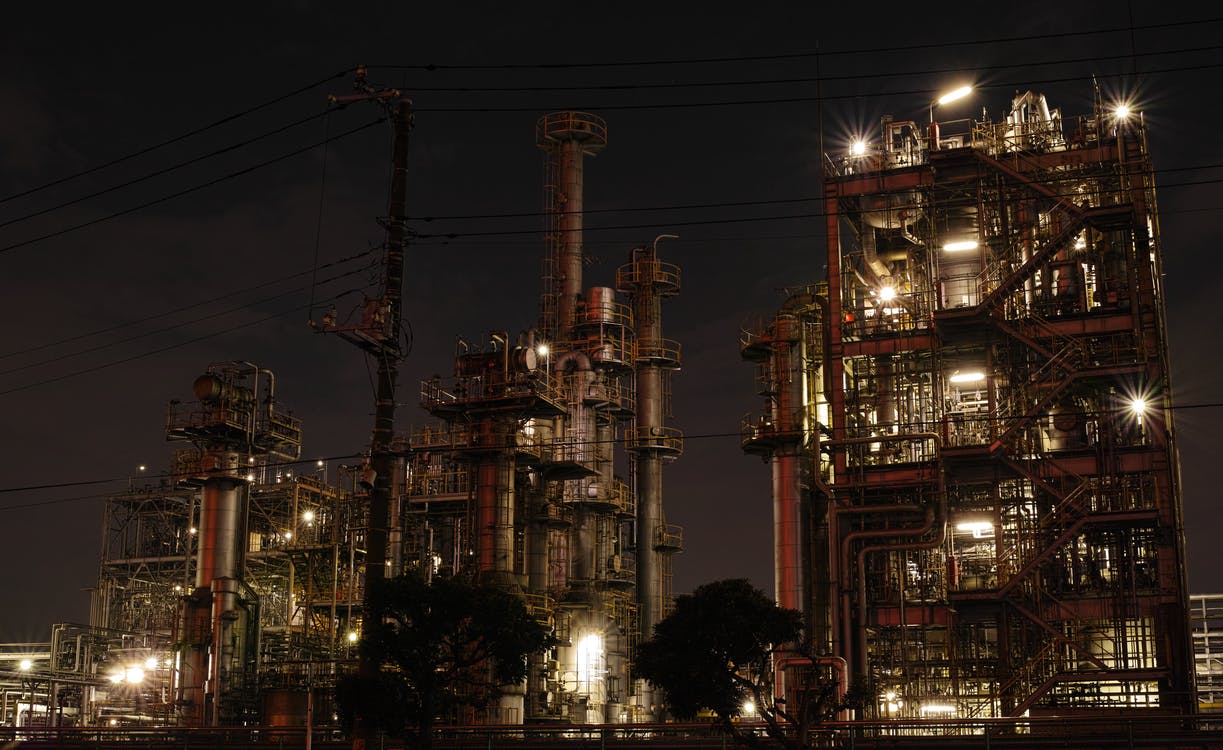
In today’s competitive business environment, companies are constantly responding to shifting customer demand as choice becomes the prerequisite for purchase.
A company’s success is often linked to its efficiency, hence visibility across the plant floor and extending in to the supply chain is a necessity. To keep pace with this competitive environment and the ever-increasing customer demands, every stage of the manufacturing process is facing the digital revolution. Soon the digitised manufacturing plant and its supporting supply chain will be a common occurrence where every key process and activity is visible in real or near time.
Zebra’s recently released Manufacturing Vision Study reveals the changing landscape, the drivers behind the changes, and the digital transformation journey to a fully connected factory.
The Zebra study found that manufacturers are planning to meet the challenges of the next five years by increasing investment in a host of new technologies to bring goods faster to market, to address burgeoning complexity, and to improve connected visibility throughout their facilities.
Although manufacturers pledged to increase their investment, almost half say the complexity of these technologies (49%) is a barrier to achieving a fully connected factory, in addition to budget constraints (43%) and integration with legacy systems (39%). The research revealed that nearly two-thirds of manufacturers are embracing smart technologies to achieve a fully connected factory by 2022.
However, even with this adoption, only 43% of manufacturers are using smart technologies today. The research indicates that 62% use pen and paper to track vital manufacturing steps, putting companies at significant risk for error. Ultimately, this number is expected to decrease to one in five by 2022 with the implementation of technologies such as barcodes, radio-frequency identification (RFID) and mobile or wearable devices.
What does that mean for the changing manufacturing industry, and how can a manufacturer make the change from pen and paper to augmented reality (AR) and robotics or wearables?
The Industrial Internet of Things (IIoT) is at the heart of this transformation. Manufacturers are welcoming in a new era of productivity by enhancing Industry 4.0, powered by IIoT. Workers are using a combination of barcode, RFID , wearables, automated systems, and other innovative technologies to track the physical processes of the manufacturing plant floor and allow companies to make decisions based on higher visibility with IIoT. Real-time monitoring across the entire manufacturing process is predicted to increase 21% by 2022.
An example of this is placing more barcode scanning points across the production process as activities are undertaken or parts are consumed to form an assembly. This is simple to execute as they become standard operating practice and afford the business incredible visibility. Time to undertake activities and parts consumed are verified at the point of assembly rather than at a quality check point before shipment, to name just two. Manufacturing is in the midst of managing huge increases in product variety to accommodate the consumers’ quest for personalisation. Hence, quality management was the number one concern – 58% for all our study respondents.
Role of Wearables
As the manufacturing industry moves a step closer toward automation, wearables will begin to play an even greater role in operations. Two in five manufacturers have promised to increase capital investment in wearable technology by 2022 but, even so, wearables are still a new concept in the manufacturing industry. Wearables are practical in scenarios where looking up data is accompanied by the need to not take your eyes or hands off the activity in play to view data / information at the same time.
Yet, many firms are willing to take the plunge. They say they will increase the deployment of wearable technology by 15% over the next five years because they want to increase real-time monitoring across production. Companies say monitoring will rise from 7% to 21% in order to improve quality assurance. Wearables will offer opportunities to increase productivity on the plant floor, as well as improve safety. Employees equipped with video camera glasses can also record what’s happening on the production line. Wearables could even monitor a worker’s health and alert supervisors if issues arise that could be considered a hazard.
Turning to IIoT and Mobilising your Workforce
Today, 27 % of manufacturers are collecting data from production, supply chain and workers. The data is stored in silos, which in turn means there are few opportunities to generate insights. However, that number is expected to drop to 19% by 2022, signaling that this situation will be resolved by connecting those silos and the importance of access to the type of data needed to improve productivity, efficiency and streamline operations.
This is where IIoT can play a role by enabling data capture across the enterprise. For example, making the inventory on-hand status visible and immediately available to plant floor managers and suppliers will improve operational performance.
Having instant access to data via the Manufacturing Execution System (MES) is essential to making real-time adjustments that ensure that the production process operates smoothly. It gives suppliers the opportunity to react to the changing needs of their customers while also keeping less inventory on-hand and can eliminating points of failure as processes are tracked effectively. In fact, 50 percent of manufacturers stated that improving their ability to adjust to fluctuating market demands is one of their top business growth strategies.
What is RFID?
One of the ways manufacturers are implementing the use of IIoT is through the use of RFID tags attached to assets, inventory or staff (via ID card) to track data and increase visibility and efficiency across the production process. RFID provides greater density of visibility and hence is dependent on the manufacturers’ visibility needs can be scaled accordingly between barcode and RFID. These technologies also offer high velocity of throughput when compared to manual- and paper-based activities.
For production to be efficient, businesses require a high-performance wireless network to provide an always-on connection. Smart sensors, such as RFID tags and location technology, make it easier to automate the collection of data, and to monitor the status of work in process (WIP), goods and locate items. All of this must be supported by a separate back office system which simplifies data analysis to support better decisions and offers better, real-time visibility over things like the stock position, resource allocation and WIP status.
RFID smart tags hold significantly more information than barcodes and are a better defense against counterfeiting. That is why industries with high value products such as textiles, pharmaceuticals or luxury goods rely on RFID smart tags to track stock.
RFID tags also help employees in the warehouse to measure size and weight. During the loading process, a forklift loaded with stock that is RFID tagged can measure the proportions and weight of a package, which also enables the more efficient loading of trucks.
Factories supported by IoT will continue to digitally transform and guide the future of industry. This transformation is where real-time communication between the supply chain and the production line will drive factory automation. A connected plant floor has become a necessity for ensuring high-quality, cost-effective production. And with rising customer demands for product variety, transforming operations isn’t something that manufacturers can ignore if they want to remain competitive in an ever-changing environment. Ultimately, there is a significant role for the IIoT-enabled factory in the future of manufacturing.
For more information, visit www.zebra.com