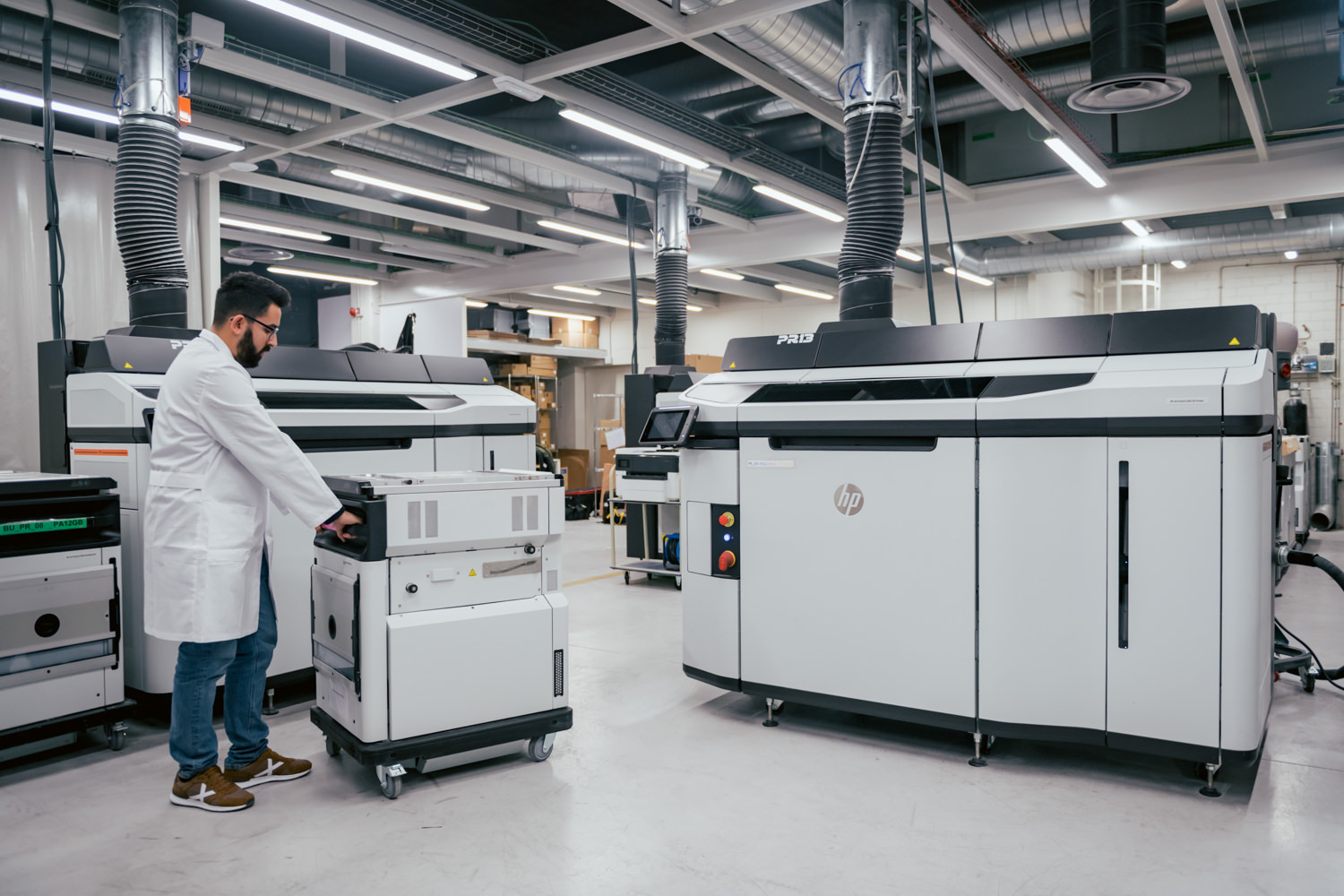
Additive manufacturing, or 3D Printing has long been trumpeted as the lodestar of a “Fourth Revolution”. In reality, uptake has been limited, it remains somewhat niche, and hype has not met market expectations. Yet as the world grapples with the COVID-19 pandemic, the 3D printing industry and hobbyists alike are stepping up to help ease the supply chain disruptions by creating and printing urgently needed components.
The major issue for healthcare workers at the moment is the overwhelming numbers of people that are in urgent need of oxygenation; requiring ventilators so they can breathe long enough for their immune system to fight off the worst of the virus.
Yet healthcare institutions are just simply not prepared for this demand and as supply chains are disrupted, many parts or equipment cannot be replaced at pace.
By now, famously, this what happened to a hospital in Italy which ran out of valve replacements for reanimation devices. They contacted the supplier, but they were unable to source any replacement valves in the time. Upon hearing this Massimo Temporelli, founder of The FabLab in Milan reached out to the 3D printing firm Isinnova, which quickly brought a 3D printer to a hospital in Northern Italy and began printing the urgently needed valves.
Open-Source 3D Printed Medical Parts
3D printing involves using a filament extrusion system to layer plastic or metals in a controlled manner. In recent years there has been sustained shift toward commercialisation of the technology at the retail level, with many hobbyists building or buying 3D printing devices that can make small plastic objects or machine components.
Now that community is springing into action to help alleviate the pressure on healthcare workers and provide them with lifesaving personal protection gear: In Ireland, for example, members of the 3D printing community are using an open source design for a Prusa 3D printer to create full face visors that can be used by frontline staff.
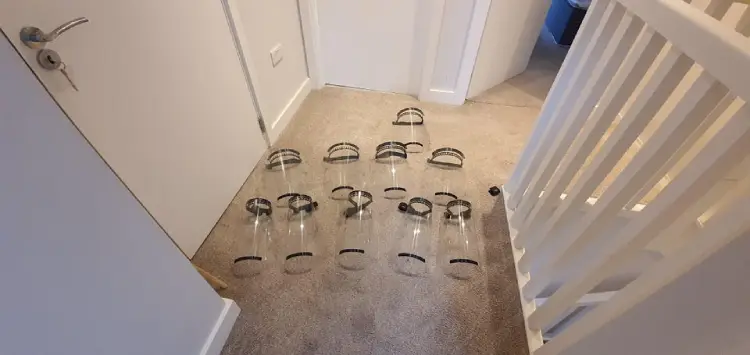
Daniel Mooney has just finished making several visors – that are being sent to the Mater hospital in Dublin – using an open-source design that was first developed by a doctor in the Czech Republic. Mooney commented in a Reddit post that: “The guys loved them and had a little feedback on the size of the visors but are happy to take as many as I can produce. Currently I’m limited to making 16 per day as my 3D printer is a bottleneck so I’m going to buy a second printer.”
However, there are limitations to this type of manufacturing process. The 3D printer is capable of creating the head mount and supports, but the actual clear pieces of PETG plastic sheets are harder to come by. As such he is reaching out to businesses in the community noting that: “Hobbies and professionals are now mass producing protective face shields in advance of lack of supply and we would like your support (businesses) in reproducing the below design in 0.5-1mm clear PETG.”
Other hobbyists have created the design plans for 3D printed face masks that can be fitted with filtration systems. Many of these designs have been uploaded to the Makerbot Thingiverse, an open-source library for 3D printer designs.
Regulators are scrambling to adapt stringent rules to accomodate this kind of support: in the US, the CDC has relaxed all rules around unapproved mask usage in healthcare settings.
Industry and Engineering Staff Try to Ease Supply Chain Pressure
Engineers at the Polish-based industrial 3D printer manufacturers Urbicum are creating a last resort ventilator system that can be printed any place in the world using basic parts. The ventilator is incredibly robust and can be powered by a car battery.
They have created a prototype that can be constructed in 15 hours using printed parts and very common industrial components.
Major Blue Chips Are Also Getting Involved
Another project that is in development by major 3D printer supplier HP is a field ventilator that can be made out of 3D printed parts and rapidly constructed. The mechanical bag valve mask could be a lifesaving piece of frontline equipment.
HP’s 3D and R&D centres in the EU, US and Canada are working to increase their production capabilities and create 3D printed components that are in short supply, the company said this week, with CEO Enrique Lores commenting: “HP and our digital manufacturing partners are working non-stop in the battle against this unprecedented virus. We are collaborating across borders and industries to identify the parts most in need, validate the designs, and begin 3D printing them.”

And it’s not all about ventilators: the firm’s network of manufacturing partners are working to create a number of unexpectedly vital 3D printed parts; from hands-free door opener devices that allow you to open doors with your elbow, to face shields and masks adjusters.
Whether this surge in attention can be sustained after the outbreak remains an open question. But with businesses around the company — not just in the medical sector — facing supply chain disruption, the agility afforded by the ability to dynamically print small and if needed customised batches of complex parts, rather than relying on distant specialist components manufacturers, looks increasingly enticing.
3D printing may just have got the lift it needed: companies that have typically used small scale machines to print prototypes are switching to production. With machines now able to print more 3D parts as well as plastic ones, Deloitte anticipates that metal will overtake plastics and represent more than half of all 3D printing this year.
Yet major structural challenges remain: 3D printing is still hugely more expensive per part than using already heavily automated CNC (Computer Numerical Control) machines, whether those are lathes, laser or waterjets. For now however, attention has refocussed on 3D printing’s possibilities, and that might just save lives.