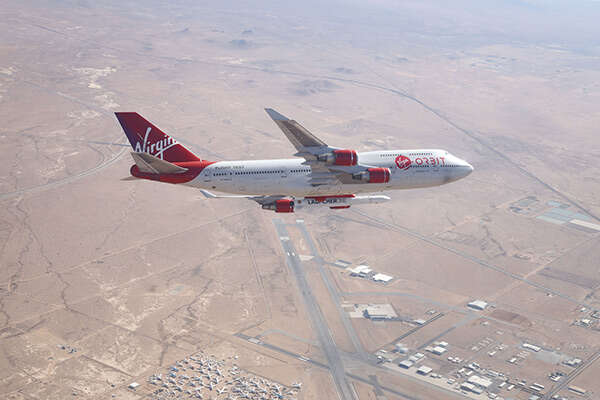
The first-ever orbital UK space launch is due to blast off later today, and if all goes to plan will help send nine satellites into orbit. One of these belongs to Welsh start-up SpaceForge, which believes it can manufacture semiconductors and other electronic components high above the Earth in a more efficient manner, while helping businesses reduce their carbon footprint.

SpaceForge is not alone in its belief that the future of manufacturing is in space. “We need to take all heavy industry, all polluting industry, and move it into space,” declared Amazon founder Jeff Bezos soon after landing back on Earth following his short trip off the planet last year.
The theory stands that by taking heavy industry into orbit you can free the planet of harmful greenhouse gas emissions, but it comes with its own challenges, not least how to get raw materials into space cleanly, and then return the materials you produce back to Earth when they’re ready.
Enter Josh Western and Andrew Bacon. The pair founded SpaceForge in 2018 after leaving European engineering giant Thales Alenia Space where they worked on developing “advanced concepts” from mining asteroids to lunar bases with the goal of making space work for humanity.
“My job was to pitch and sell these ideas,” Western says. “We had as much success as you would anticipate having in such a big company.” That led to the pair sitting down together to think about ideas that might work as a start-up – and SpaceForge was born.
“We met a couple of times in the pub to discuss how crazy we were. And then we started in a garage on the outskirts of Bristol with a 3D printer and a vacuum pump. Over the course of one summer we built 13 or 15 different prototypes,” explained Western, who said even then the goal was sustainability including tracking their carbon footprint.
“We have been calculating our CO2 emissions from day one,” Western says. “The first time we ordered a Domino’s to that garage we even calculated the CO2 emissions of getting the pizza. The aim is to be carbon negative when we are fully operational.”
In the five years since it was founded, the company has gone on to have one of the largest seed funding rounds for a space start-up in Europe ($10.2m) and moved to a building in Wales where a team of more than 40 full-time staff are working on satellites that can be used to make components and then return to Earth safely for re-use.
“We’re on the edge of an industrial estate in Cardiff,” says Western of SpaceForge’s HQ. “Until last summer it was building burger vans for funfairs. Where the fridge for the burger patties used to stand is now our clean room, phonics lab, mechanical workshop, payload integration and design.”
SpaceForge is ready for the UK space launch
SpaceForge is now ready to send its first test satellite into space. ForgeStar-0 will be launching from Virgin Orbit’s Cosmic Girl, a Boeing 747-400 aircraft that flies to 35,000ft before deploying a small rocket and its payload into orbit. The launch is from Spaceport Cornwall and is due to take place today. It will be the first time a rocket has launched from Europe.
Dan Hart, CEO of Virgin Orbit told Tech Monitor there is an environmental benefit to launching in your own backyard. “There is also a logistics benefit of that,” he adds. “There are several benefits and there’s a local economic benefit where the support activities for the spacecraft, for the integration can come from the local area.
“We’re excited to be working in Cornwall and bringing space technology there. We’re reusing a 747, we’re reusing a runway. We look forward to using sustainable aircraft fuel on our 747 and perhaps as we go forward even in our rocket engines.”
He said SpaceForge was the type of company that could benefit from local launch capacity, by having it close by for a more rapid launch and return, without the need to transport satellites around the world first.
Several satellites are launching alongside the SpaceForge test spacecraft. The launch, known as “Start Me Up” will include a maritime awareness satellite, a pair of MoD cubesats, a satellite for improving GPS in the UK and Oman’s first orbital mission.
What comes next for SpaceForge?
In the future SpaceForge plans to launch up to 12 times per year, manufacture in orbit and return to the Earth, coming down off the coast of England after it completes its work in orbit. There are real benefits to orbital manufacturing, says Western.
“Space offers a much better manufacturing baseline for almost any material,” he says. “The Earth is a wonderful place to live, but a terrible place to try and make anything else. If we are able to transition industry away from earth and into space, even small niche parts of it, we can enable really an enormous paradigm shift when it comes to basically how we think about how humans interact with our natural environment.”
The first spacecraft is designed to launch with raw materials on board, take them to low Earth orbit and use the power of the Sun to turn them into a usable component, then return to the Earth but there “will be a very quick transition from one generation to the next”.
The challenge for Western is to get the environmental cost down and that includes the emissions from launch, the raw materials and computing power. “Our biggest use of carbon is cloud computing right now,” he explained. “The amount of modelling, simulation, mission planning and stuff we do is incredibly computationally intensively.”
With a plan for a dozen missions per year, and Spaceport Cornwall self-limited to just 14 space launches per year SpaceForge will look further afield for its next launch, sometimes launching multiple satellites at once on “rideshare” missions like those operated by Elon Musk’s SpaceX.
“We might take the opportunity to batch some missions up, perhaps for a quarter instead of monthly,” says Western. “We would have some in a kind of a holding pattern or almost asleep. Some will be operational producing materials, some will be on the return journey, and then be refurbished in our factory.”
The reason for this is to achieve a frequency that matches the demand from customers for components, allowing SpaceForge to fit within the current supply chain rather than requiring existing companies to change processes and patterns. “I mean, if we needed everybody to make a design change to work with the products we made, then we’d be looking at a much longer life or even design time before we had a benefit,” he says.
The era of Microgravity-as-a-Service
Part of the wider project is to launch Microgravity-as-a-Service, bringing the low gravity environment of near-Earth space to a wider market than is possible with the International Space Station, and then bring the experiments, materials and projects back to Earth for more advanced analysis.
The satellites will operate at about 800km above the Earth, still classed as low Earth orbit, which Western says is a “sweet spot” where the balance of vacuum, low gravity and ease of return to Earth is just right for orbital manufacturing. This is twice the altitude of the 400km International Space Station orbit and higher than the thousands of SpaceX Starlink communications satellites, which orbit at about 550km.
“We have a higher purity vacuum access because we’re away from Earth and we’re away from the contaminated orbit of the space station. But we’re close enough home that it’s a relatively simple return manoeuvre to come back,” Western says.
There are already customers lined up for the first flight, but not for materials produced on the satellite. The customers are a secondary business for SpaceForge and include research and development payloads for companies and institutions looking to leverage the benefits of low gravity and vacuum conditions.
“Nobody was providing the infrastructure to continually access that environment,” said Western. “So what we’ve seen in the past three-six months, is we’ve had a lot of reach out from researchers, academic institutes and even commercial research divisions of everything from pharmaceuticals to fast-moving consumer goods.”
On the test flight there will be a material sample for a US company and a laser tracking technology demonstration developed in the UK. While it won’t return to Earth this time, Western says it will provide valuable insight for when they do return the spacecraft.
The tracking technology is by the British start-up Cosmic Shielding Corporation. Its Plasteel radiation shielding technology aboard will launch on ForgeStar-0, the name of the test spacecraft, and could be the basis of future return missions, making it easier to bring materials back to the Earth safely.
Regulation stopped SpaceForge from bringing this first spacecraft back to Earth. “We reached a position with the European Space Agency, the UK Space Agency and our Civil Aviation Authority, where we were asked the question, ‘what happens if this goes wrong?’,” said Western explaining the need for caution.
“We demonstrated all of the simulations, all of the modelling and various architectures within the tools that they prescribe you use and demonstrated that it is in fact safer than a lot of other satellites.” But due to the nature of the return mission, unusual among spacecraft, it was felt that an in-space test was required.
“What it is going to do is demonstrate an element of our re-entry technology. We’re going to then run this mission through a variety of scenarios demonstrating different failure modes before it eventually completely fails and we just have the standard platform demise. This is really the final step for us to demonstrate how our technology performs if it does not perform correctly.”