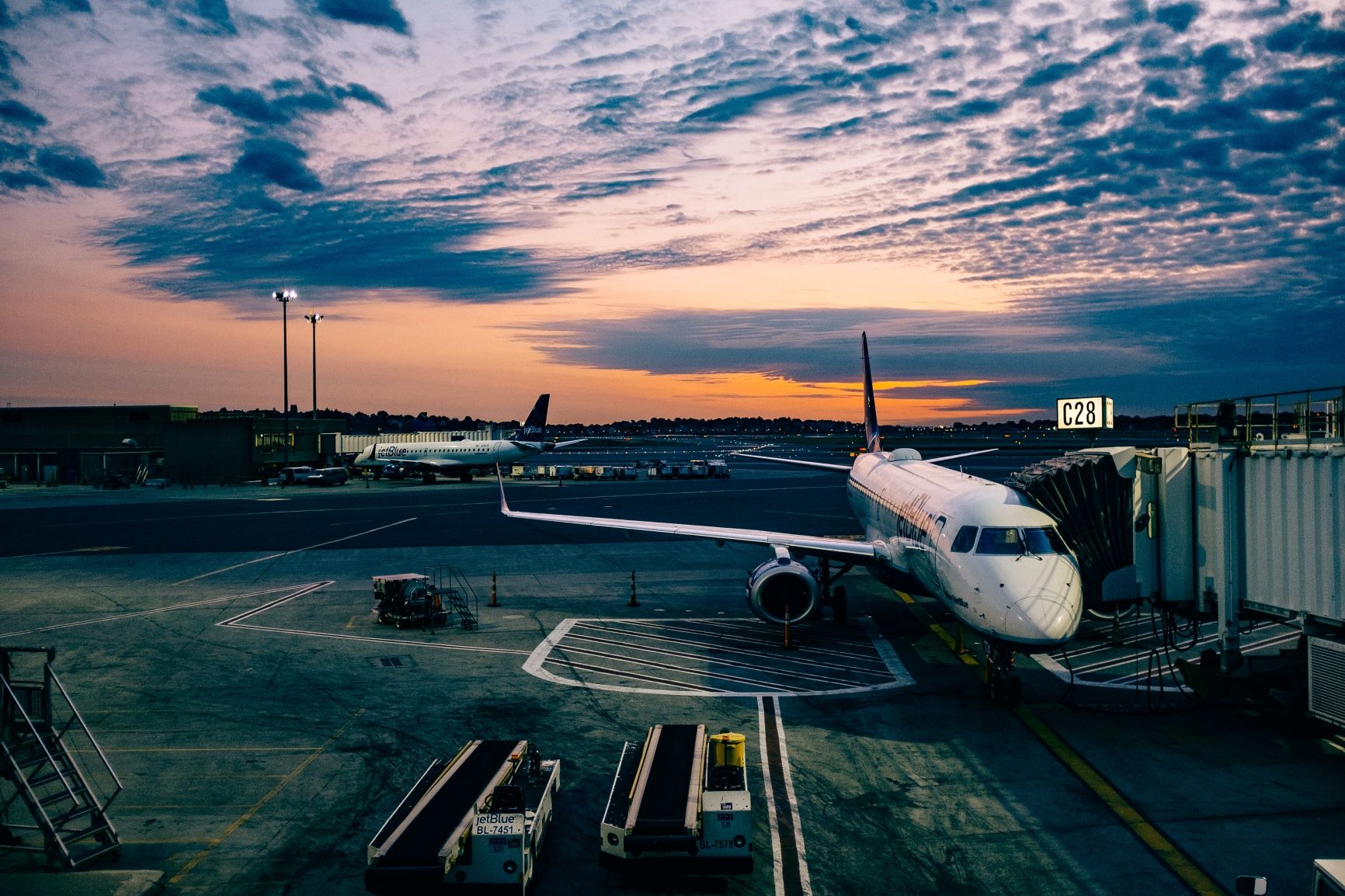
I’m sure that engineers in all industries will make the same claim, but maintenance in the commercial aviation industry is of utmost importance. The need to fulfill rigorous safety standards and the downstream impacts of any errors in aircraft maintenance have positioned this topic front and centre for manufacturers and airline operators, writes Graham Grose, Aerospace & Defense Industry Director at IFS.
Safety first, yes, but profits a close second: many current approaches to aircraft maintenance also having a significant impact on the revenue streams of airline operators. In 2017, for example, airlines spent a combined $76 billion on maintenance, repair and overhaul, representing around 11 percent of total operational costs.
Reacting to engineering problems as and when they occur causes delays and disruption in flight schedules, lengthens waiting times for sourcing parts, and presents barriers to effective and timely communication between all parties in the aviation ecosystem. The impact of delays and disruptions can be felt widely, having a knock-on effect on areas such as inventory allocation, schedule planning and supply chain optimisation.

Digital evolution: the must-haves
The need for predictive maintenance is just one of a list of ‘must-haves’ if the industry is to evolve en masse to becoming digital, intelligent and fully connected. Customer service and experience, for instance, can be improved with ultra-personalised pricing and insights gathered via sentiment analysis on social media. Flight delays and cancellations can be forecast more accurately, flights re-booked, schedules altered and resources re-allocated. Airport processes such as baggage processing, meanwhile, can be made more efficient via facial recognition technology.
Customer experience is a core element of most aviation businesses, but it is ultimately dependent on the ability of those businesses to actually operate a safe, reliable, profitable service in the first place. This takes us back to the need for predictive maintenance for digital transformation in the industry. Why have many business leaders found it so difficult to evolve their operations in this regard? Ironically, the very cornerstone of digital transformation has also posed a barrier to companies seeking to adopt digital-first strategies: data.
By 2026, the amount of data generated by global fleets will hit 98 billion gigabytes, with new aircraft generating up to 80 times what older planes do today. This is a huge amount of intelligence which can be mined for insight and will be crucial to predict faults, monitor engines and limited life parts in real time, and rectify issues on-the-fly. However, these benefits will only be felt if airlines are able to harness this data effectively – indeed, we’ll only actually reach this digital, data-rich aviation future if airlines harness data more effectively.
Manual Processes No More
Despite aircraft becoming more and more sophisticated and technologically advanced, many in the aviation industry still use spreadsheets and manual, paper-based processes to manage the way these assets are maintained. Huge investment has gone into the technology and innovation which has resulted in ultra-fast speeds and feats of engineering; now, the same level of investment must go to the tools working behind-the-scenes to make the most of these aircraft.
This means making sense of data: gaining complete visibility of an aircraft’s performance, and collecting, analysing and managing this data in real time. Using predictive maintenance software with embedded AI capabilities, airline operators can more effectively consolidate data across an entire fleet, support accurate long-term planning and help engineers react faster to change. New tasks, engineering orders or aircraft can be introduced to a maintenance programme quickly and easily.
This dynamic approach to planning reduces risk, and gives the organisation the level of control required to predict and plan as effectively as possible in what is a constantly changing business environment stringently underpinned by compliance and regulation.
Predicting the Future
In addition to dynamism and immediacy in maintenance and planning, AI-embedded maintenance and engineering technologies also allow operators to act and solve problems immediately. Such systems are able to harvest data from aircraft operations (such as engines) automatically, and then push maintenance programme changes back to the operator. As a result, life-limited engine part maintenance deadlines can be updated based on actual operating conditions and life consumed by each engine in use.

Engines and limited life parts can also be monitored whilst the plane is in the air, allowing an operator to rectify any issues as soon as the aircraft comes to the terminal stand. This mitigates the need to take planes out of service, thus minimizing unnecessary delays and cancellations – both of which come at huge expense to an airline.
This is an approach taken recently by aero-engine manufacturer Rolls-Royce, which is using an AI-powered solution to analyse the performance of fleets using its engines. The company then goes one step further, using this insight to improve the aftermarket offerings it can provide its customers, from service-based contracts to analytics insights and more.
Which brings us to the final benefit of AI for aviation. Rather than just providing the hardware (in Rolls-Royce’s case, the engine), manufacturers can also pursue service-based business models. Supporting airline operators throughout and beyond the sale of a product will provide these businesses with a better quality of service, and manufacturers with a long-term and lucrative revenue stream.
Business leaders need to act now to help propel the commercial aviation industry into the digital-first future – and they need the tools to facilitate this. AI is a trend, but it’s also an enabler of predictive maintenance, accurate planning, and cost reduction. Ultimately giving flight to the best possible customer experience.