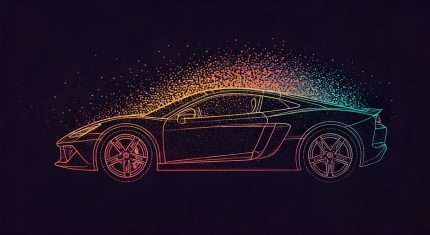
The truly successful product, goes the saying, is either “fast, good, or cheap.” That adage rings true across all sectors, but especially the automotive industry. Indeed, designers working in the world’s largest car companies are under constant pressure to deliver on all three qualities, all without compromising on safety.
Take autonomous vehicles (AVs). Engineers aren’t just building cars anymore, but nodes in complex networks that need to operate perfectly at all times. Even partially autonomous solutions like advanced driver assistance systems (ADAS) must protect drivers, passengers, and pedestrians through highly connected systems that trigger instant reflexes. And it’s not all about the vehicles themselves – a component as small, and as crucial, as vehicle lighting faces similar challenges. Design cycles are shortening, but safety remains paramount.
Traditionally, manufacturers have relied on physical prototypes and real-world testing, but this approach is becoming the antithesis of speedy development. Additionally, engineers will struggle to develop and test highly complex systems if they’re working with physical components. It should surprise none, then, that simulation is emerging as the new future of automotive innovation.
Advancing ADAS capabilities
One topic central to automotive innovation is autonomy. A combination of ongoing development and public concerns around safety, however, has meant that AVs aren’t yet the new norm. To bridge the gap and encourage consumer trust, manufacturers have been putting their focus on ADAS features, such as adaptive cruise control, traffic sign recognition, and blind spot detection.
ADAS features offer the best of both worlds: they assist and protect while still allowing for human oversight. To enable this, sensors such as lidar, radar and cameras are used to improve a vehicle’s awareness and help it ‘see’ and react in real time. If a child unexpectedly runs in front of the vehicle, for example, onboard sensors will detect them and automatically brake. As such, the design challenge comes in knitting together the highly complex and interconnected system that underpins ADAS. It’s virtually impossible to achieve this without the use of digital technologies.
Simulation engineering is what makes ADAS possible. Engineers can digitally design, test, and validate not only the sensors but also the entire connected system, ensuring it operates safely and effectively. Any number of virtual scenarios can be deployed to predict the system’s behaviour so that it can respond appropriately in a real-world environment – and if it makes an error, engineers have the visibility to understand the why and how, and adjust accordingly, without setting foot on a physical road. And this digital-first approach doesn’t just help bolster confidence in ADAS: it can play an instrumental role in bringing AVs into the mainstream.
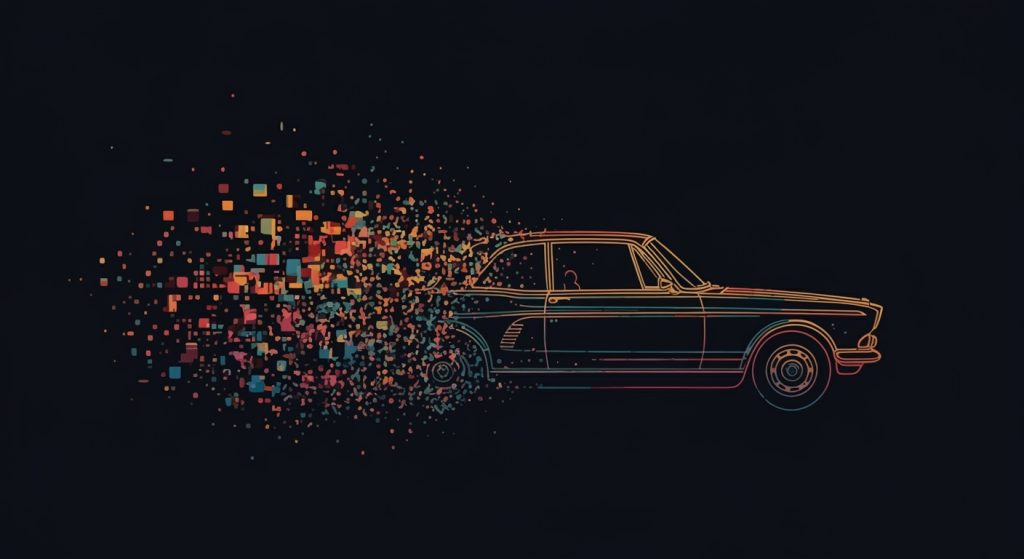
Digital twins unlocking full automotive autonomy
ADAS, powered by simulation, takes the world one step closer to full automotive autonomy. But for consumers, going from partial assistance to full machine control is still a great leap forward. Manufacturers need to demonstrate that AVs are as accurate as possible – not just to soothe public fears, but to adhere to increasingly strict standards and regulations.
This is where simulation – specifically digital twins – can be of value. A digital twin is a virtual replica of a real-world product. It’s updated in real-time to constantly mirror its physical counterpart through data collected using embedded sensors. This makes the twin a highly accurate model and a game-changer for predictive maintenance and product optimisation.
Adding generative AI to the mix advances matters even further, reducing the length of training sessions from days to mere seconds and improving the end model’s capacity for real-time decision-making.
This is invaluable for an AV. Such a vehicle, after all, needs to know how to operate in different terrains and weather conditions, navigate and mitigate risks, and generally be prepared to face any sort of unpredictable situation. Naturally, physical testing is out of the equation – but simulating all these scenarios is still time-consuming. AI, however, can accelerate this process, training an AV on billions of miles of scenarios whilst still remaining grounded in the laws of physics through the digital twin. As a result, organisations can mitigate AI hallucinations, accelerate development, and bolster consumer trust in AVs.
Drilling down into lighting
There are some incredibly exciting developments happening in the automotive space. And while digital twins can bring these innovations to life, their benefits also extend to the more ordinary components of a car. Lighting is one example – it showcases the vehicle’s presence, helps driver navigation, and can ultimately prevent accidents in the dark. Though it may not be as exciting as, say, ADAS, it is no doubt crucial for a vehicle’s design and safety.
Optical systems come with a host of challenges, and it’s not just about the aesthetics. Lights need to be bright but energy efficient, robust against all potential weather scenarios and vibrations from the vehicle, and should illuminate without blinding others, even at high-beam. And, of course, there are safety regulations to comply with. Simply put, if lights are too bright or too dull, they can put the public at risk and cause miscommunications between drivers.
Engineers can take a few different approaches with simulation here. The tech can be used to drill down into optics and support with developing photonic components, or it can be leveraged to design and model a vehicle’s entire lighting system. In the testing stage, simulation can mimic human visual perception and real-world variables to ensure lighting is effective but safe. On a broader level, engineers can use simulation to integrate a lighting system into the overall vehicle design to ensure interoperability between components and validate safety against external standards.
The automotive sector is not short of design challenges, so having a comprehensive solution is crucial. Whether organisations are bringing next-generation vehicles to the road, or working on the smallest vehicle components, every element must operate as safely and effectively as possible. By leveraging simulation, they can overcome almost any challenge – and usher in a new era of innovation for the industry.
Kishor Ramaswamy is a director of application engineering in optics at Ansys.