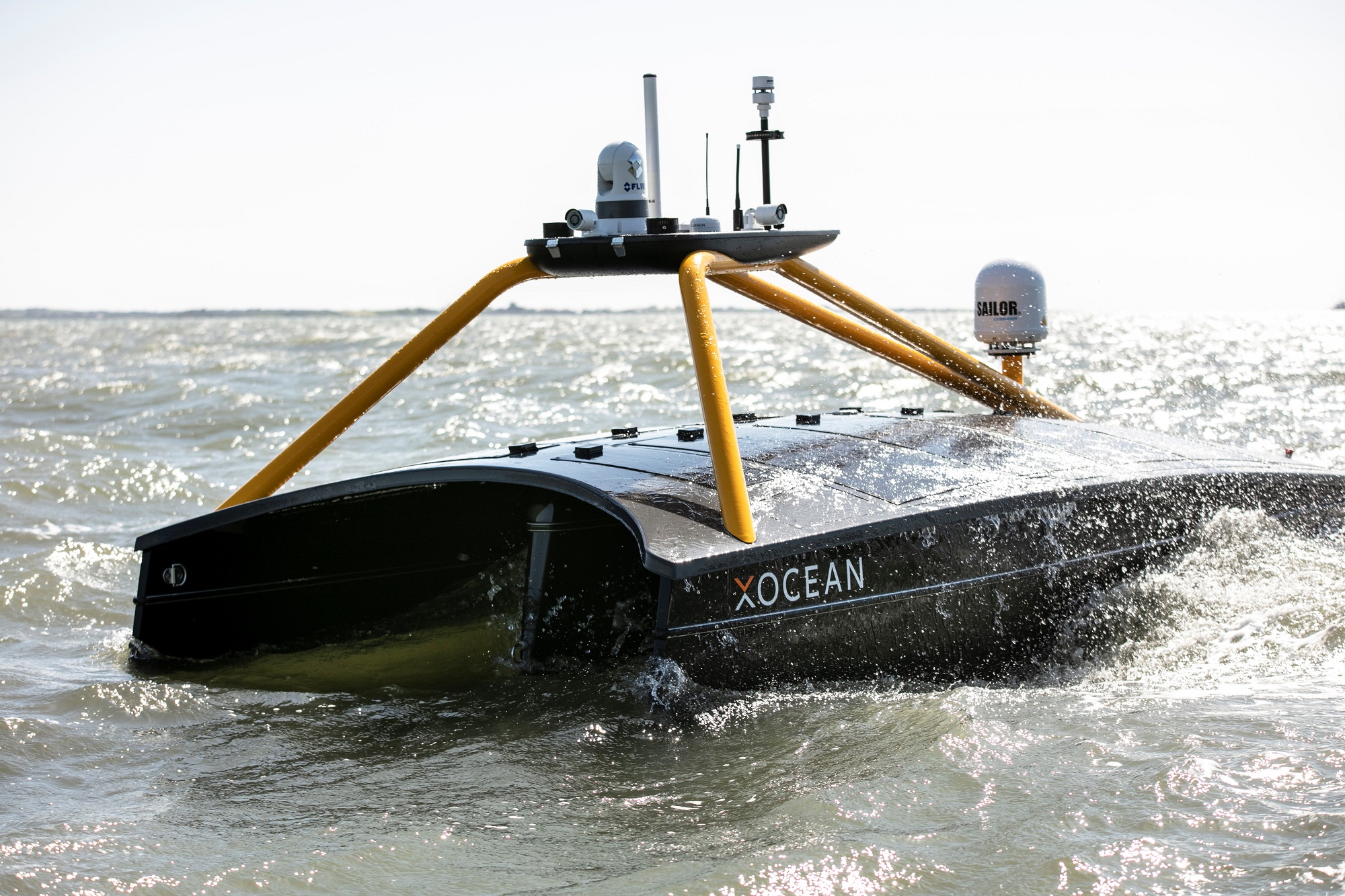
Billions of dollars worth of infrastructure sits in the world’s oceans. Offshore oil rigs, undersea telecommunications cables, wind farms and wave energy converters: any damage to these assets can be highly disruptive, expensive and dangerous to fix, and environmentally disastrous. This need to maintain high standards, cost-effectively and in extreme conditions, is prompting ocean asset operators to explore the frontiers of automation and artificial intelligence (AI).
Oil rig operators are under particular pressure, as oil prices plummet. “Current operating models and organisational models are unsustainable,” says Tony Edwards, CEO of Stepchange Global, a digital transformation consultancy that specialises in the oil and gas sector.
“Operators are looking to maximise production as well as significantly drop opex and capex,” Edwards told delegates at the recent Digital Energy Leaders Summit. “Many operators have already pulled the traditional levers and are now looking at how they get the next level of performance.”
Scanning the seas for data insights
Just as flying drones are used to inspect buildings and other land-based infrastructure, uncrewed surface vessels are increasingly deployed to monitor ocean-based assets. XOCEAN is an Irish start-up that makes remote-controlled boats which can scan the seas, collect data and monitor valuable assets. They are operated remotely from dry land via satellite broadband link.
“We see ourselves as an ocean data company,” says CEO James Ives. “The thing that we deliver to our customers is data, but we do this with uncrewed vehicles rather than conventional ships.”
XOCEAN’s customers include governments, energy and utilities companies and telecommunications providers, that use the system to monitor infrastructure such as pipelines and undersea cables.
“Asset integrity inspection is a growing market for us,” Ives says. “We’ve worked with BP and completed thousands of kilometres of ultra-high-resolution surveying of their pipelines using sonar.
“We look for things like whether ocean bed has moved around the pipeline, whether any debris has landed on it, things like that.”
Using USVs is safer, cheaper and has a lower carbon footprint than traditional data collection methods, says Ives.
“During the first lockdown we did a project monitoring sensors in Norway with Shell,” he says. “We sent the USV by freight, had a local partner unpack and launch it for us, and our team was sitting in Ireland controlling the craft that was hundreds of kilometres offshore.”
Engineers from the sensor provider were able to log in over a secure connection from England and communicate with their sensors on the seabed, with XOCEAN feeding information in near real-time to the Shell teams in Norway and Houston.
“We’ve delivered projects all over the world without a single person having to step foot on an aeroplane, and that can be really transformational because the carbon footprint is negligible.”
Autonomous drones protecting oil rigs
XOCEAN’s USVs float on the surface but some ocean infrastructure requires underwater inspection. Needless to say, this is highly skilled and dangerous work.
ORCA Hub is the world’s largest centre for research into robotics technology for offshore energy infrastructure. A collaboration between five universities and 30 industry partners, the hub is developing robotic devices that can inspect and even repair underwater assets without the need for human control.
“Our solutions are designed to support those working in the field of offshore energy and minimise the risks posed to humans,” says Dr Sen Wang, associate professor in robotics and autonomous systems at the National Robotarium at Heriot-Watt University, and a contributor to the project.
These underwater drones are equipped with smart stereo cameras, inertial sensors and sonar to detect the environment around them. “These sensors use AI algorithms to understand the environment and plan a path for an inspection,” says Wang.
The hub is also developing autonomous flying drones for use on offshore wind turbines. “Drones are currently used to visually inspect offshore wind turbines, but these inspections are remotely controlled by people on-site at the offshore location,” explains Professor Mirko Kovac, director of the aerial robotics laboratory at Imperial College London.
If an issue is identified, human technicians are often required to carry out further investigations and repairs in extremely challenging environments. An autonomous system could save time, money and cut risks.
“As well as visually inspecting a turbine for integrity concerns, ours make contact, placing sensors on the infrastructure, or acting as a sensor itself, to assess the health of each asset,” says Professor Kovac.
“Our technology could even deposit repair material for certain types of damage.”
Drilling into the benefits of digital twins
These new sensing devices add to the growing volume of data that ocean infrastructure operators collect about the performance and condition of their assets. Analysing that data to optimise operations and plan maintenance requires new techniques as well.
Offshore drilling giant Seadrill is integrating AI to optimise its oilrig operations. “Adding in AI means we can more easily harness all the information from various sensors and devices to draw actionable insights that are not otherwise identifiable with traditional applications and business intelligence solutions,” explains CIO Jennifer Hohman.
For example, the company uses AI to plan its rig maintenance. Previously the company had a regular repair schedule which didn’t take changes in drilling conditions into account. This meant that parts would be replaced before their useful life had expired. Now, conditions are monitored and analysed in real time, and replacement schedules are updated automatically.
To ensure wells are situated in right place and the right configuration, Seadrill simulates potential drilling sites with digital twin technology. This allows it to model the environment and the impact of fluctuating sea conditions on its infrastructure.
Much of this analysis takes place in the cloud, of course. But given that its rigs are connected via satellite links, Seadrill has taken a “hybrid” approach to data processing, Hohman says, with some information collected on the rigs processed at the edge, and larger data sets sent to the cloud.
The next frontier of analysis, Hohman says, is the ‘red zone’, where employees come into proximity with the drilling equipment, and therefore where the risk of injury is greatest. Seadrill already deploys lidar, used by self-driving cars to navigate the roads, to monitor the positioning of people and equipment, and in future plans to develop this to help automatically detect and prevent potential collisions – another example of how the need to maintain safety in extreme conditions is pushing ocean infrastructure operators to the cutting edge of AI and automation.