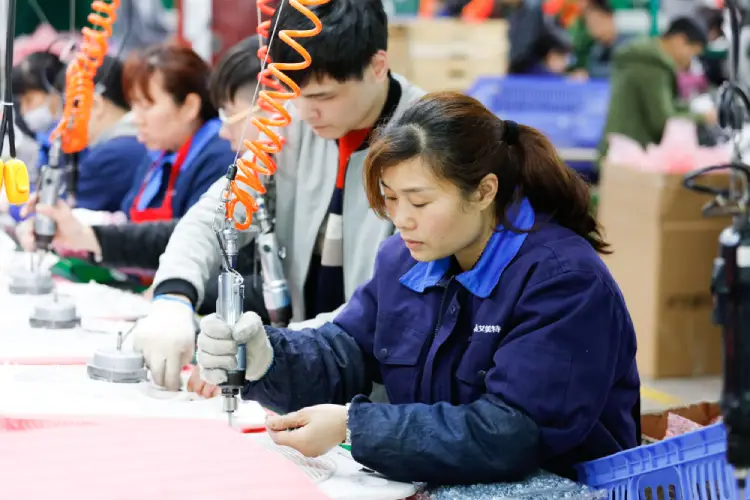
Covid-19 increased demand for automation but the economic uncertainty it unleashed prevented companies from investing. This ‘pent-up’ demand is expected to accelerate automation from next year onwards. This could offset as much as half of the economic damage caused by the pandemic, researchers say, but only if it is matched by an acceleration in reskilling. Governments are beginning to take action but none on the same scale as China, which is positioning itself to be the biggest winner from automation in the next decade.
Automation and upskilling
Covid-19 has had a devastating impact on economic growth around the world. But countries could recoup as much as half of these economic losses by making workers more productive through automation, says PwC chief economist Jonathan Gillham.
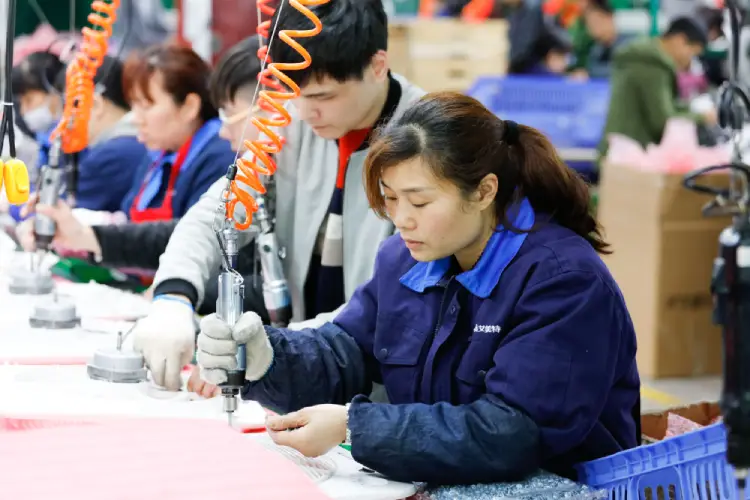
“What the Covid crisis has done is shown people that this actually can be done, and it can be done at pace, because people were forced to adapt their working practices to survive and a lot of people did that through the adoption of technology,” he says. “There’s been a large economic hole that’s opened up and one way to help close that is to make the workforce more productive and upskill them.”
For this productivity boost to happen, any uptick in automation needs to be matched by upskilling (giving workers the skills to conduct higher-value tasks) or reskilling (helping them do other things entirely) so that workers can be effectively redeployed alongside this new technology. The World Economic Forum (WEF) estimates that half of all employees worldwide will need reskilling by 2025 due to automation.
The investment that employers and governments make in skills development will determine the economic impact of automation, according to a report by the WEF and PwC. In an accelerated scenario – where the necessary investments in reskilling and upskilling are completed by 2028, compared with a core case of closing this skills gap by 2030 – automation could boost global GDP by $6.5 trillion over the next decade, the equivalent of adding twice the UK’s GDP to global output.
Unfortunately, in much of the world, this is not happening. The WEF’s Future of Jobs Survey found that half of all businesses were accelerating automation as a result of the pandemic, but that only just over a third were accelerating their reskilling initiatives, risking a situation where workers miss out from the gains from automation.
Indeed, the survey points to a misalignment between the interests of employers and employees, with 43% of companies expecting to downsize their workforce by 2025, compared with only 35% expecting to expand it; however, with skills shortages as the top barrier to automation – identified by over half of businesses – there is clearly an acute need to ramp up spending on reskilling.
Without investments in reskilling, automation will drive inequality between workers and between companies, says Till Leopold, head of frontier insights at the World Economic Forum (WEF).
“The double disruption from Covid [and automation] has the big risk of increasing inequality, not just between workers but also between companies that have the capital to invest in all this digital infrastructure and smaller companies that are being left behind,” he says.
“[But progress] is driven by the investment decisions that companies and governments are taking today, and so this is also very much something that is within our control. [Covid-19 has] accelerated the challenge, but possibly the situation has also helped to focus minds onto the solution as well.”
China’s automation opportunity
The gains from automation are unlikely to be spread evenly around the world. The country with the most to gain is China because of its large but ageing workforce, considerable skills gap and ballooning domestic market.
In an accelerated automation scenario, China will add 7.5% to its GDP by 2030, according to PwC analysis. This is an “absolutely plausible” prediction given the high levels of investment that the country has already undertaken, says Gillham.
“Countries that invest in a big way and quite early could really start to see massive gains; you’ve got some really big outliers there at the top,” he says. “One of the key advantages for China, in particular, is that it’s actually manufacturing a lot of technology that will underpin this upskilling revolution [and] if you’re engaged right from the bottom of the supply chain, you’re more likely to be able to effectively implement it as well.”
That is not to say China will not be challenged by the oncoming wave of automation. Over 500 billion worker hours will be displaced by automation by 2030, according to research from McKinsey – the equivalent of 87 days a year for the average worker. Meeting the accompanying surge in demand for technical, social, and higher cognitive skills will require a radical shake-up of the economy and of China’s education system, which was designed for a bygone era of industrialisation.
McKinsey predicts a surge in demand for roles demanding high levels of technical competency, such as “frontier innovators” and skilled professionals, while construction, manufacturing and agriculture roles will be replaced by automation. To meet this reconfiguration of the skills market, McKinsey expects one-third of global reskilling efforts will occur in China, representing the displacement of 220 million workers in the mid-point automation scenario.
There are also huge gains to be made in other parts of the developing world. Starting from a much lower skills base than the global north, regions of sub-Saharan Africa and Latin America could see similar gains to China, according to PwC’s analysis.
But these countries also face many more structural challenges, says Gillham. “For middle-income or less developed economies, the risk factor of adopting these types of technologies can sometimes be higher because perhaps a low proportion of the customer base might have access to Wi-Fi and the internet,” he says. “[But] what some of these technologies have helped is with countries to jump stages of development.”
Policy approaches to reskilling
The economic opportunity posed by automation has been acknowledged by governments around the world, and feature heavily in national Covid-19 recovery plans.
Some are tackling the skills challenge too. Luxembourg has introduced a “digital skills bridge” initiative to funnel investment towards retraining workers in emerging technologies, while the UK government has announced a Lifetime Skills Guarantee to reshape the tertiary education system to cope with the demands of automation.
Other policy approaches include “jobs commissions” to incentivise companies and local authorities to upskill the young and the recently unemployed; new shorter and more agile training courses for reskilling the displaced; and a reconfiguration of education systems to align learning more closely with employment outcomes, the WEF says.
It is crucial governments engage with this issue sooner rather than later, warns the WEF’s Leopold, as decision made now will shape the global workforce for the coming decade. “We have an opportunity here to really improve the quality of many of the jobs that have been perhaps precarious in the past, and to really raise the floor for everyone,” he says. “But left on its own we could see that vicious downward cycle of the de-skilling of jobs, with automation taking an ever-bigger bite out of what’s left for humans.”