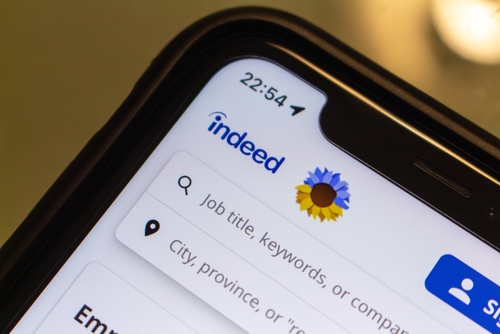
3.8 million roles need filling in the US within the next decade to fulfil evolving tech manufacturing demands, a new report finds. With growing need for new digital skills and roles, Deloitte predicts that half of the skilled open positions (1.9 million) might not be filled if efforts to bridge the talent gap aren’t made.
Deloitte and the Manufacturing Talent Institute highligh these findings in a new report, “Taking charge: Manufacturers support growth with active workforce strategies”. It addresses what is being done to fix the talent gap, and what is still needed to get there, citing upskilling through e-learning platforms and mentoring, and initiatives to attract talent through additional employee support and opportunities among the solutions.
“The manufacturing industry is facing exponential opportunity, yet still should prioritise strategies that will address the skills and applicant gap, especially as the acceleration of digital skills-based jobs continues,” says John Coykendall, principal and vice chair of US industrial products and construction leader at Deloitte Consulting.
“Developing talent — both from within the existing employee base and those newly entering the workforce — is important to keeping up with the pace of continued innovation. Companies who invest in upskilling the workforce through training, technology and policies that meet employee expectations are well-positioned for future growth.”
The study highlights three key themes. Firstly, industry growth is driving demand for workers across all manufacturing roles, from entry-level to highly skilled production roles and engineers. Skill requirements are also evolving across technical manufacturing skills, digital and soft skills. Lastly, closing the skills gap is hindered by a shortage of potential candidates applying for roles, meaning manufacturers should work harder to retain and upskill their existing talent.
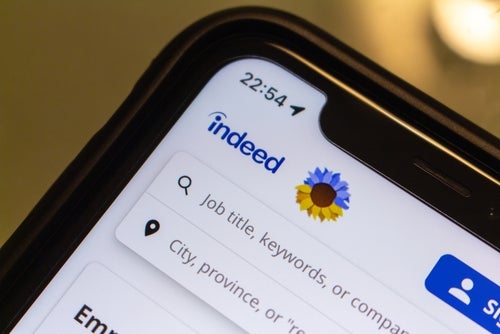
New demand for digital roles and skills
The report also highlights that AI, data analysis, and big data will be critical in the future of manufacturing, with one out of two respondents citing familiarity with these applications as important to very critical, while another 40% consider it as a good to have, mostly for engineers, technicians, operations personnel and maintenance technicians.
The growing demand for digital skills in manufacturing is said be largely due to the increasing complexity of operations and products, and the need to integrate and analyse information from smart connected devices and systems. The requirements for soft skills, “such as critical thinking, problem-solving and creativity underpin others that have seen growth”, such as customer service, said the report.
The report found that there has been a 75% rise in demand for simulation and related software skills over the last five years, mostly needed for technology-enabled production or testing roles. It also predicts that roles such as statisticians, data scientists, engineers, logisticians, computer and information system managers, software developers and industrial maintenance technicians will most likely experience the most growth from 2022 to 2032.
The fastest-growing production roles are most likely to require higher-level skills such as semiconductor processing technicians, machinists, first-line supervisors, welders, and electronics and electromechanical assemblers.
Growth expected in the manufacturing industry
The study began in December 2023, marking Deloitte and The Manufacturing Institute’s sixth manufacturing talent study over two decades. It involved a survey of over 200 US manufacturers, interviews with more than 10 senior executives from manufacturing organisations across different sizes and sectors, and an extensive review of secondary data on labour supply and demand.
Deloitte’s economics team supported the study, which conducted proprietary analysis on labour supply and demand data to explore the potential impact of unfilled jobs on the nation’s economy. The study analysed manufacturing job descriptions and growth trends and involved a focused analysis of over 80 manufacturing companies’ annual reports and investor presentations.
Other findings in the report involve expected growth in the manufacturing industry, higher-level skills likely to be required for industry 4.0, a “customer focus” and further investment in partnerships with a regional approach.
The workforce is evolving
“Manufacturers recognise that the workforce is evolving. Pandemic-driven shifts have already created hundreds of thousands of new jobs, and now we are seeing increased demand for digital skills that need to be met or risk further widening of the talent gap,” said Carolyn Lee, president and executive director of The Manufacturing Institute.
“Companies must prioritise technology, training and talent development, and the investments that are driving growth will also require the industry to build out a talent ecosystem. With investments in partnerships, apprenticeships, and education, and prioritising a more diverse and inclusive workforce, a whole host of new talent will be on the factory floor and driving the next wave of growth.”