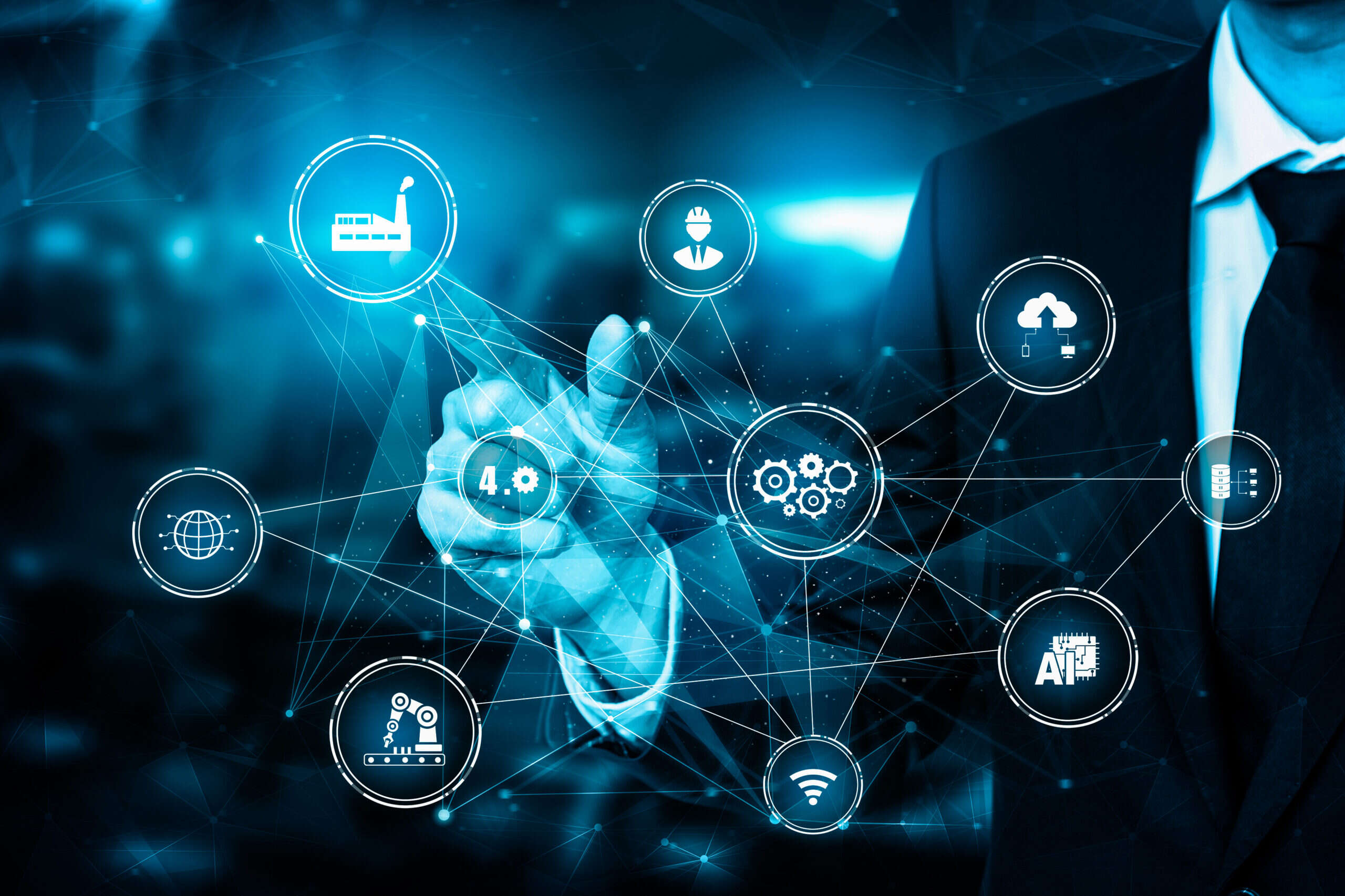
Manufacturers are no longer facing difficult choices between sustainability and efficiency, with digital technologies driving the adoption of new ways of working which allow businesses to save money and cut their carbon footprint.
As the fourth industrial revolution (4IR) becomes a reality, manufacturing companies are deploying sensors and utilising data in their facilities to help meet sustainability goals.
The World Economic Forum (WEF) tracks companies at the forefront of this work through its Global Lighthouse Network, which is run in partnership with McKinsey. The network comprises over 100 manufacturers deploying 4IR technologies at scale, and provides a forum to share ideas and best practices.

It cites the example of a consumer healthcare company which was able to couple advanced controls with green technology to deploy a sensor-fed automated system to cut energy consumption, resulting in 25% less energy consumed and an 18% reduction in CO2 from its facilities.
“Companies no longer have to choose competitiveness or sustainability because smart manufacturing lets them achieve both,” said Enno de Boer, a partner at McKinsey who leads on the consultancy’s manufacturing work. “Fourth industrial revolution technologies – think artificial intelligence, robotics and the internet of things – amplify human capability and technological innovation to accelerate sustainability while also strengthening competitiveness.”
A report produced by McKinsey for the WEF, Unlocking Sustainability through Fourth Industrial Revolution Technologies, outlines some of the technologies being deployed in factories in the Lighthouse Network.
The most common are IoT systems, with sensors and data visualization being used to monitor equipment performance and provide information resource consumption. Factories are also setting up digital twins to “create dynamic energy models that recommend how to optimize high-energy consumption processes”, the report says. Advanced analytics can power real-time energy management systems capable of auto-adjusting settings as necessary.
The report also identifies technologies which can have indirect sustainability benefits. Digital delivery optimization can be used to consolidate shipments, in turn providing emissions benefits. Meanwhile, “artificial intelligence-enabled process improvement utilises automation software to improve workflow and traceability alongside flexible real-time resourcing to eliminate human error in the product lifecycle”. This can reduce the amount of waste emanating from a process.
Cisco Meraki is able to support manufacturers deploying 4IR technologies and making the transition to smarter ways of working. Its secure, intelligent, and cloud-first IT automates time-consuming operations, ensures agility in the face of unexpected challenges, and leverages built-in analytical insights to deliver exceptional experiences.
The company’s MT sensor range provides comprehensive environmental monitoring, while the MV smart camera range can help with location analytics and smart building automation, and can be connected via the 802.3at PoE Injector, which allows power and data to flow down a single ethernet cable. Meanwhile Meraki’s cloud-first WiFi also enables energy savings. Built on the WiFi 6 standard, itcan optimise network performance as capacity, traffic, and utilization changes, allowing connected devices to operate more efficiently.
The company’s comprehensive ecosystem of turnkey partner apps allows manufacturers to rapidly scale out solutions for asset tracking, site safety, quality control, remote operations, sustainable operations and much more with minimal effort and time, all of which can contribute to meeting sustainability targets.
- Find out more at https://meraki.cisco.com/experiences/smart-spaces/