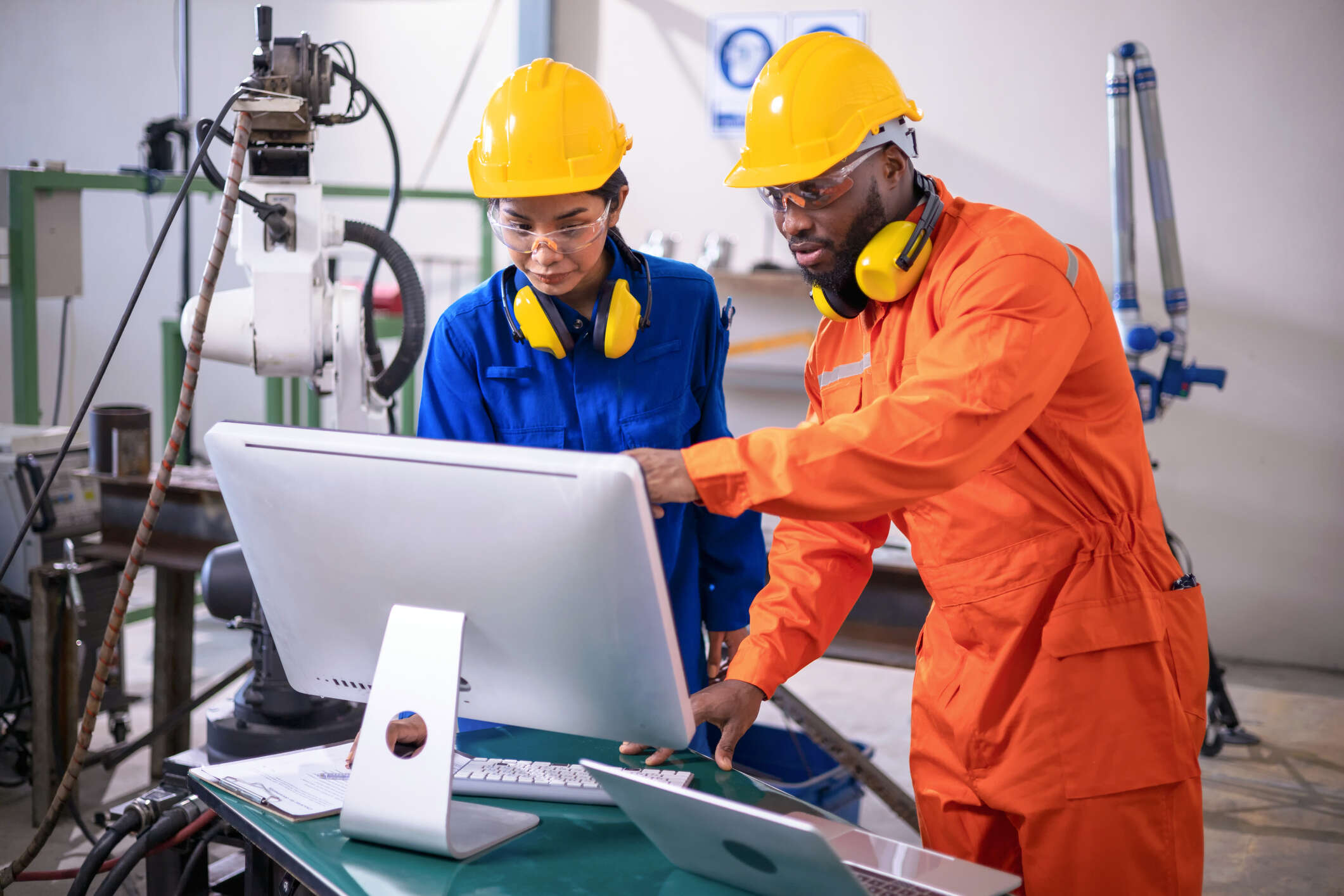
Whether it is geopolitical trends that dramatically change relationships between major trading markets, a global pandemic, or even war, the events of the last two years have brought unprecedented challenges to every industry. For manufacturers, just as one challenge starts to fade into the background, another seems to emerge. In many cases, traditional manufacturing solutions for managing one’s business no longer reflect the requirements of the new normal.
“In terms of the pressures on UK manufacturing, nothing in the past prepared us for the events of the last three years,” says Andrew Kinder, SVP strategy at Infor, a global leader in business cloud software products. “First Brexit, then Covid, and then the impact of war in Ukraine. Each has left its own distinct mark on the manufacturing sector.”

Though Brexit is not new, and talk of its effects was quickly overtaken by the outbreak of Covid-19, it made the movement of goods between the UK and the European mainland more complex and, crucially, much more expensive – particularly for smaller businesses.
“Smaller businesses were just not used to the form-filling that comes with ‘exporting’ to the EU,” Kinder says. “All of a sudden, there are imposed administration and costs that businesses didn’t have before and in many cases these same businesses did not have the staff or automated systems that larger manufacturers had to mitigate costs.
“Then there was pandemic, which shut down global demand for many industries and brought about furlough for others. The impact was instant and a stuttering return through 2021 and 2022 has been difficult to manage.”
The effects of the pandemic are still keenly felt in the world of manufacturing and more broadly in the market for international trade. There are many material shortages, notably silicon chips, electrical components, metals and many food ingredients, creating significant output issues.
“The UK car industry, for example, finished the first three months of 2022 100,000 vehicles down on where it was a year ago,” Kinder observes. “That’s its own sort of long Covid.”
Nevertheless, it is fair to say that the world is starting to come out of the shadow of the pandemic, or at least return to some kind of new normal way of living, working and trading. The resurgence of global demand, however, has sparked dramatic energy price increases, greatly impacting costs for manufacturing businesses, and further exacerbated by the outbreak of war in Ukraine.
Russia’s invasion, a war on resources
Apart from creating a humanitarian crisis in Eastern Europe, Russia’s invasion of Ukraine in February has had a profound impact across the globe. Energy prices worldwide have soared as a result, as have the prices of other essential commodities.
“Added to the increased energy costs there are also shortages of many critical materials; Ukraine is a major global supplier of wheat, corn and barley; and both Ukraine and Russia are major suppliers of iron and steel,” says Kinder. “It’s also becoming increasingly difficult to navigate the ethics of trading in Russia, with many businesses re-assessing their trading positions.
“There are other macro-economic trends that have not necessarily hit the headlines, but are also important” he adds. “One of them is labour scarcity, partly due to the ageing demographic that’s affecting Western and Eastern economies. By 2030, the baby boomers in the UK will be over 65, and in the US by 2034, older adults [over 65] will outnumber children [under 18] for the first time in its history.
“Sources of lower cost labour are being exhausted. There isn’t another China, there isn’t another Eastern Europe. It’s the end of an era. The retreat from globalisation, which started prior to Covid has been accelerated.”
Added to this is the need to operate in a more sustainable fashion, as manufacturers have a pivotal role to play in addressing the impending climate crisis, as manufacturing is the source of at least one-quarter of global emissions.
After decades of plentiful and relatively inexpensive labour, cheaper raw materials, lower energy prices and, for the UK, free access to its major trading partners, manufacturers are facing a confluence of circumstances that is forcing a rethink of their processes, practices, partnerships and technological infrastructure in the search for efficiency and better margins.
A time for change to smart manufacturing processes
Now is the time for manufacturers to act not only to limit the impact of these big challenges but also to become key actors in reimagining the manufacturing supply chain.
“Manufacturers are innovators,” says Kinder. “They are already finding ways to reduce, reuse, refurbish, and recycle their products. The supply chain is changing. Now, it’s not just about ‘fabricate and forget’; it is about what happens when the product is at the end of its life. Many businesses have set themselves a ‘net zero’ target and are looking at everything from design, to responsible sourcing, to recycling as part of a sustainable business model.”
So how can manufacturers not only respond to these pressures, but also grasp the opportunities that lie within and beyond them? One practical step is to look to how modern technologies can help through increased automation and speed of response.
“Resiliency trumps efficiency” Kinder remarks, “and technology can play an enormous role in building an agile and resilient business. Take supply chain for example; a recent survey from MakeUK showed that over 40% of manufacturers were already using digital connectivity to improve visibility in the supply chain and around a third are using technologies that predict or anticipate changes.”
Other technologies such as cloud-based systems have also been an important driver in accelerating agility by bringing affordable cutting-edge solutions to smaller manufacturers that don’t have the benefit of large IT teams.
Infor has focused on helping manufacturers meet their evolving industry needs through its end-to-end ‘CloudSuite’ platform. Each Industry CloudSuite is a fully integrated, industry-specific solution tailored for example, to the needs of an automotive supplier or to a complex equipment manufacturer. “It’s not a ‘one-size-fits-all’ solution”, says Kinder. This results in faster delivery and delivery through a cloud service ensures that the customer is always taking advantage of the latest version.
“Smart manufacturing is dependent on the digital connection of machines, people and processes,” Kinder surmises. “That requires having a cloud-based technology platform that can connect, adapt and scale easily. Getting the technology platform foundation right is the first step on the journey to digitalisation and better business outcomes”.