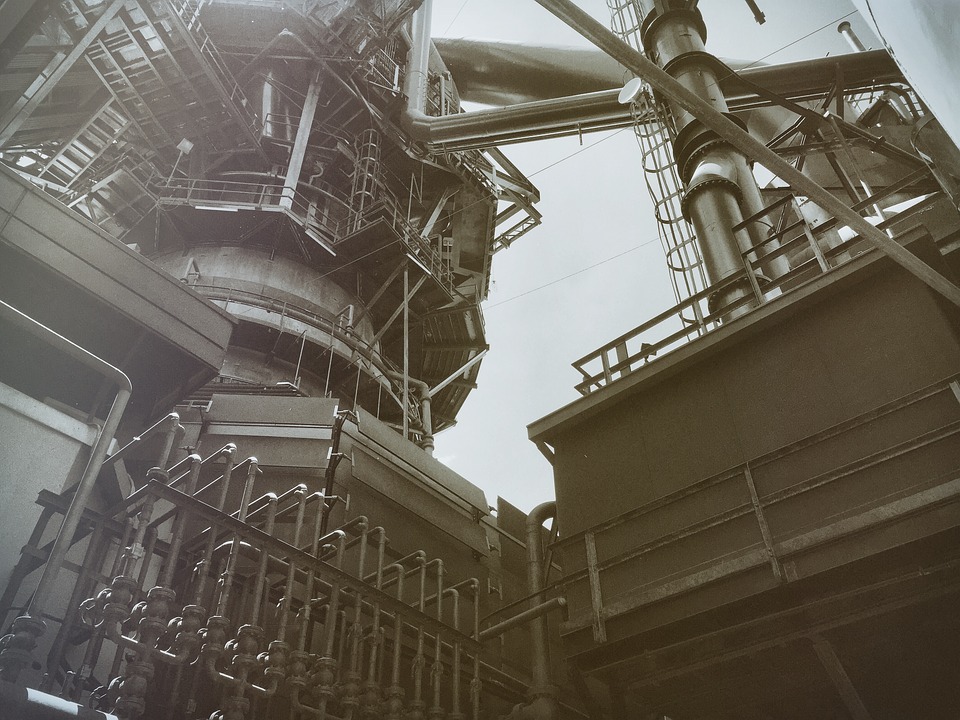
Most industries are currently undergoing a form of digital transformation, the effects of which are being experienced by businesses everywhere.
Advances in technology have changed the expectations of consumers, who now require products and services available any time and via any channel they choose.
For businesses to achieve the flexibility, agility and speed to market required to meet customer demands, they must take advantage of the opportunities made available by digitalisation to improve and transform their products and processes.
Businesses in the manufacturing sector in particular face the challenge of an increasing number of requests from customers for rapidly produced parts to be made available within days, at a level of quality that will guarantee satisfaction. As an industry under such pressure, it’s perhaps unsurprising that there’s a sense of uncertainty around the future of manufacturing.
Painting a conflicted picture
The Confederation of British Industry (CBI) reported an improvement in manufacturing order books in the three months to February 2017, as they achieved their highest level in two years. Similarly, the ONS published its UK index of production in late 2016, revealing a growth in output of more than 2 percent.
Around the same time, however, EEF, the manufacturers’ organisation, revealed that nearly half of the manufacturing executives it surveyed indicated that they thought they’d be in for a “bumpy ride” during 2017 as, according to the organisation’s CEO, Terry Scuoler, they were “forced to navigate uncertainty, unpredictable economic conditions and a number of risks that have been amplified by Brexit”.
These reports paint a conflicting picture of success for the manufacturing industry.
Flexibility, agility and speed to market
To achieve the flexibility, agility and speed to market required to remain competitive, manufacturers are turning to digitalisation and advanced manufacturing techniques to improve and transform their existing products and processes.
The evolution of digital manufacturing means the production process is faster than ever before, with customers receiving components or finished parts within a matter of days of submitting their design online.
Making the right choice
Digital manufacturing techniques—services such as 3D printing or CNC machining—are widely used by customers to develop their prototypes and parts.
CNC machining—where computers are used to control high-speed milling and turning tools—is a popular choice for customers looking to manufacture parts for industrial and commercial equipment and machinery.
Alternatively, 3D printing is more suited to projects with more complex technical requirements or part geometries. Advances in 3D printing has enabled our customers to reimagine how components are designed & finished.
Combining the two techniques can sometimes be advantageous to businesses; CNC machining can be employed as an add-on in order to fine-tune 3D printed objects, for example. Today’s manufacturers can use the two technologies in conjunction as a way of addressing ever more challenging design requirements, such as the increasing demand for lightweight components and products.
Renewed sense of confidence
Although industry reports present an uncertain outlook for manufacturing, industry practitioners are not deterred and continually drive improve their services to meet ever-evolving customer demands. Instead, by taking on board the developments in digitalisation and advanced manufacturing techniques, the manufacturing industry is placed in a position where it can face the future with a sense of confidence.